レーザ孔(穴)あけの特徴 ~材料に応じた最適なレーザ発振器の選定~
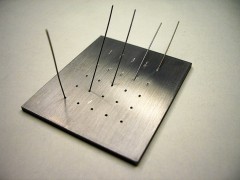
月刊ツールエンジニア 2011年11月号より
「レーザ孔(穴)あけの特徴 ~材料に応じた最適なレーザ発振器の選定~」
株式会社レーザックス 池田 剛司
1.はじめに
本誌の購読者はツールを使ったドリル加工による孔(穴)あけの知識や経験が豊富にあると思われるが、レーザ孔(穴)あけについてはどのようなイメージをお持ちであろうか。ツールの代わりにレーザ光を用いるというように置き換えれば簡単なのだが、光は質量を持たず空間を自由に行き来するし、多くの場合は目に見えない不可視光なので、想像しにくいと思われているかもしれない。ここでは、レーザ孔(穴)あけの加工方法と特徴を、レーザの種類別に説明するので、レーザを用いることのメリットを理解して頂ければ幸いである。
2.レーザ孔(穴)あけの特徴
レーザは光なので、ドリル加工などのような接触加工ではなく、非接触加工である。そのため、ワーク形状がレーザ入射方向に対して斜めであっても、曲面であっても加工でき、ワーク形状にあまり左右されない。この特徴を示す例として、三次元加工に対応したNd:YAGレーザ加工機で板厚2mmのステンレス鋼SUS304に様々な角度で加工した斜め孔(穴)あけサンプルを図1に示す。ドリル加工では斜めにツールを当てるとワーク表面に沿って逃げていくのだが、レーザでは照射した場所と方向そのままの孔(穴)が開くのである。
次の特徴は、加工対象材料が多いことである。セラミックスやガラスなどの硬くて脆い材料であっても、軟質ゴムなどの軟らかい材料であっても加工できる。ただし、材料に応じてレーザの波長を使い分ける必要がある。例えば定点でレーザを照射するシングルショットやパーカッションなどの微細な孔(穴)あけの場合、金属ならNd:YAGレーザ(波長1064nm)やファイバーレーザ(波長1070nm)、樹脂ならKrFエキシマレーザ(波長248nm)など、ガラスなら半導体励起固体レーザ(Nd:YAGレーザ等の4倍高調波で波長266nm)などがそれぞれ適切である。また、前述のレーザに加えてCO2レーザ(波長10.6μm)も候補に挙がる。
ここで、レーザ孔(穴)あけの加工方法を図2の模式図を用いて説明する。シングルショット及びパーカッションとは、定点でレーザを照射させる加工方法であるが、シングルショットはその名前が示す通り1ショットで孔(穴)あけを行う加工方法、パーカッションは複数ショットで孔(穴)あけを行う方法である。シングルショットでは短時間で孔(穴)あけできるが板厚に制約が出る一方、パーカッションは厚板の貫通孔(穴)加工で用いられる。いずれもビーム品質がそのまま影響し、ビーム径付近の直径しか加工できない。トレパニングは開けたい孔(穴)の輪郭に沿ってレーザ照射する加工方法であるため、様々な穴径や形状が加工でき、孔(穴)の位置形状の安定性の面で優れている。何周も走査することによって厚板加工が可能だが、微細孔(穴)では孔(穴)形状が崩れることもある。また、トレパニングを一筆書きのように一回の走査で連続して行うのがレーザ切断加工である。
そして最後に、加工速度を特徴として挙げる。レーザはレンズなどによって集光させることにより、高いエネルギーを小さな面積に集中させる。これにより材料の溶融・蒸発除去が爆発的に行われるため、他の加工方法に比べて加工速度が速いのである。表1に、タービンブレードへの冷却孔(穴)あけを想定し、ある条件で耐熱合金ハステロイの孔(穴)あけ加工速度を比較した例を示す。パンチングが微細孔(穴)あけに向かないこと、電子ビームが真空中で行うこと、これらを除けばレーザの孔(穴)あけ加工速度が最も速い。
以上のような特徴を持つレーザ孔(穴)あけであるが、次項からはレーザの種類別に具体例を挙げながら特徴を説明していく。
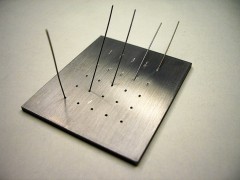
図1 Nd:YAGレーザ斜め孔(穴)あけサンプル(弊社加工事例より)
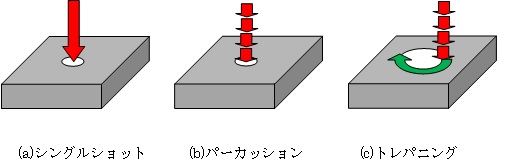
図2 レーザ孔(穴)あけ方法の模式図(著者自作)
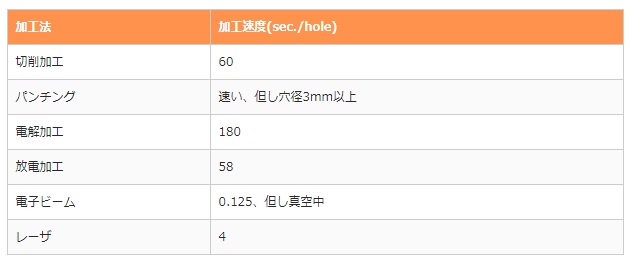
表1 ハステロイの孔(穴)あけ加工速度比較例
(高原ら、レーザによる冷却通路孔の加工技術、日本ガスタービン学会誌Vol.22 No.85 p83-89より)
3.Nd:YAGレーザによる金属孔(穴)あけ
Nd:YAGレーザでは図1に示したように金属材料に斜め孔(穴)あけが可能で、レンズを用いてレーザ光を集光することによりエネルギー密度を高くし、定点で照射するパーカッション加工により、細くて深い貫通孔(穴)加工を行う。直径0.5mm程度以下の孔(穴)あけを例にすると、鉄鋼材料では板厚25mm、アルミニウム合金や銅合金などレーザの反射が強い材料では板厚10mm、アルミナなどのセラミックスでも板厚10mmの加工事例がある。孔(穴)あけに用いられるNd:YAGレーザは、平均出力は数十~数百Wであるが、ミリ秒程度のパルス発振をさせて数十kW程度もの鋭いピーク出力を発振して材料を瞬時に溶融させる。しかし、この加工は純粋なレーザの力だけで成り立つものではない。加工機先端の、図3に示すようなアシストガスノズルから高圧のガスを吹き付けながらレーザ照射することにより溶融した金属を押し出して除去する。弊社ではアシストガスノズルの角度を変えながら加工できる三次元加工機により、航空機ジェットエンジン部品の冷却孔(穴)あけを行っている。また、別の加工機で図4に示すように直径3mmのステンレス鋼SUS304パイプに狭ピッチで直径0.5mmの孔(穴)あけを行った例を紹介する。このような加工事例を活かして医療機器のステントが製作されている。ドリル加工とは異なり、レーザは加工時に材料に力が加わらないので、このような繊細な加工が可能である。
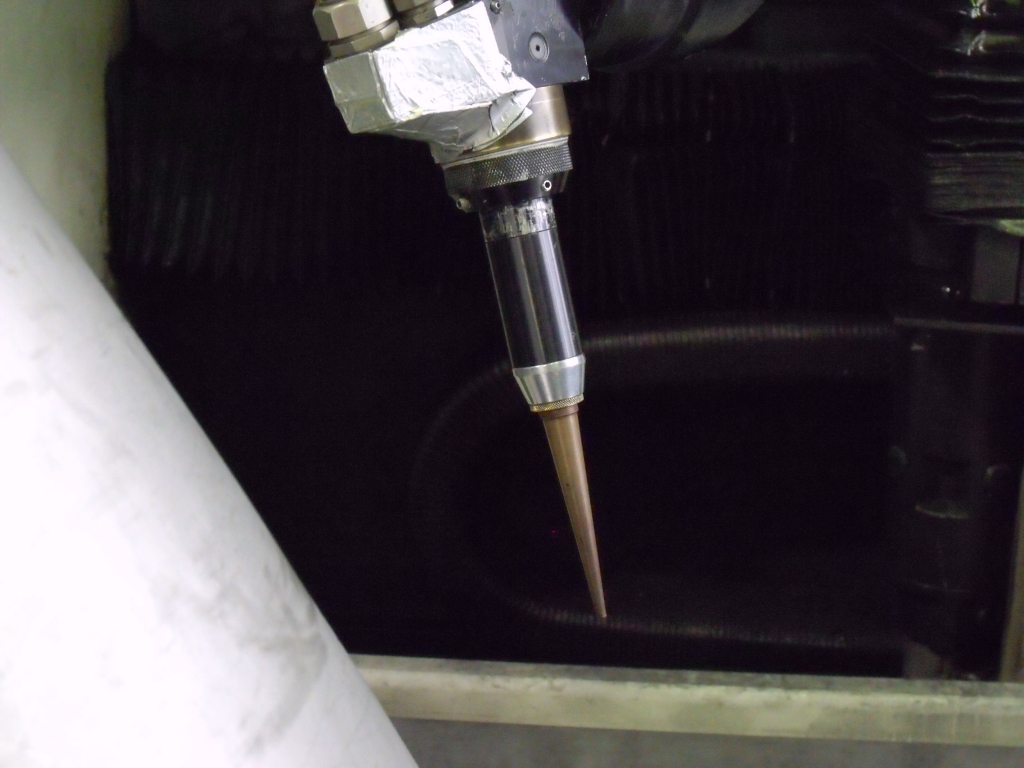
3図3 Nd:YAGレーザ加工機先端のアシストガスノズル(弊社加工機より)
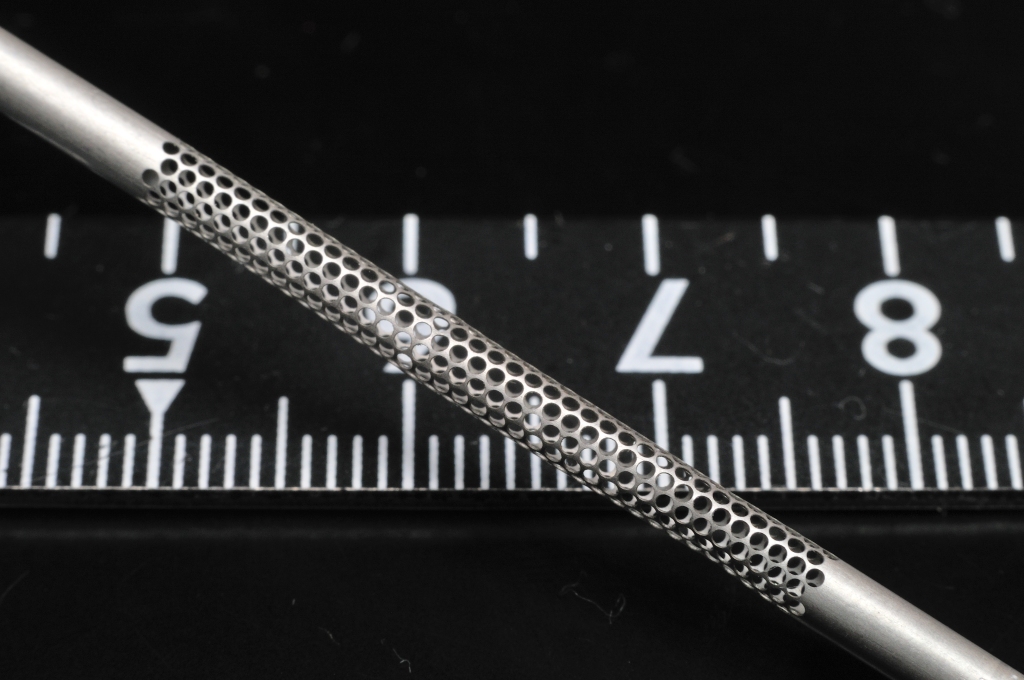
図4 Nd:YAGレーザパイプ孔(穴)あけサンプル(弊社加工事例より)
4.エキシマレーザによる樹脂孔(穴)あけ
エキシマレーザは、例えばKrFでは248nmの波長で発振するように紫外線領域の短波長であることと、数十ナノ秒という非常に短いパルス発振をさせるという特徴を持ったレーザである。波長が短ければ短いほど一般的には材料へのレーザ吸収率が高まり、効率的に熱が伝わる。また、ナノ秒という一瞬では、熱が周囲に伝わる前にレーザ照射が終了してしまうため、孔(穴)周辺の熱影響や損傷を小さくすることができる。特に樹脂材料では、金属に比べて低い温度で溶融、分解するので、一瞬にして蒸発除去される。エキシマレーザはマスク転写方式により照射するため、前述のNd:YAGレーザとは全く加工方法が異なる。その概略図を図5に示す。レンズはレーザ光を集光させるために用いるのではなく、マスク像を転写させるために用いる。図中では、レンズの焦点距離をfとして、1/A+1/B=1/f及び、A/B=L1/L2=M(=縮小率)が成立する。つまり、マスク寸法の1/Mに縮小された像がワーク上に転写される。この特徴を活かした加工事例を図6に示す。直径1.5mmのナイロン系樹脂パイプに四角形の孔(穴)を開けている。前述するようなNd:YAGレーザでは円形ビームを集光させているので円形の孔(穴)しか開けることができないが、エキシマレーザでは様々な形状の孔(穴)加工が可能である。また、円形の孔(穴)しか開けることができないドリル加工に対しても優位性がある。さらには、マスクの中に複数個の孔(穴)を開けることにより、同時多孔加工が可能なので、生産性向上につながっている事例もある。
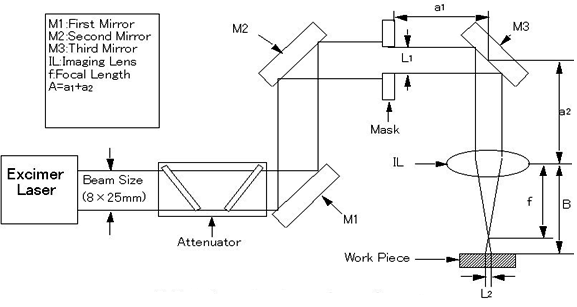
図5 エキシマレーザ加工機の概略図(著者自作)
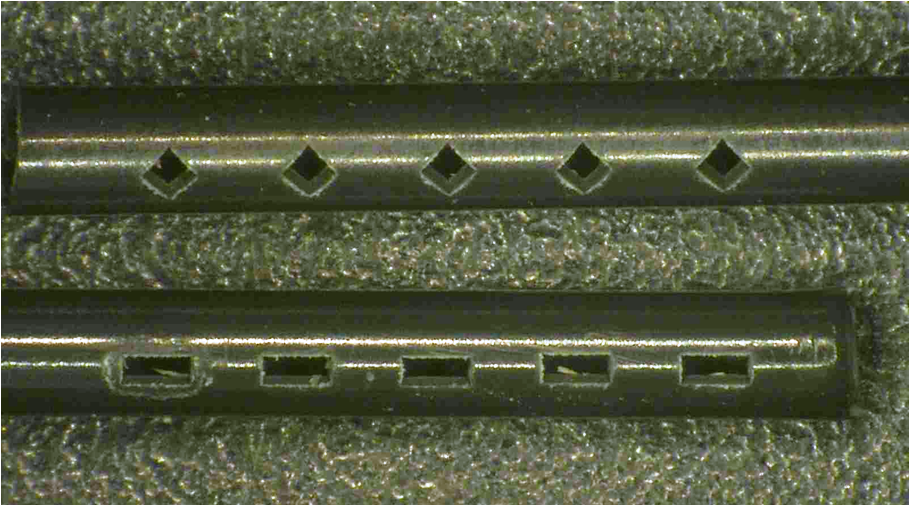
図6 エキシマレーザ樹脂パイプ孔(穴)あけサンプル(弊社加工事例より)
5.半導体励起固体レーザによるガラス孔(穴)あけ
半導体励起固体レーザは、Nd:YAGレーザ(波長1064nm)等の光が波長変換素子を経由することにより、波長532nmの2倍高調波、波長355nmの3倍高調波、及び波長266nmの4倍高調波へと波長を変換させて用いることが特徴である。その一例として、スペクトラ・フィジックス社の3倍高調波発振器を図7に示す。また、同社ではユーザ側で波長変換素子を交換可能な発振器もあるので、材料によって適した波長を適宜選択することが可能である。半導体励起固体レーザは、短波長になるほど平均出力が下がり、高くても数十W程度の平均出力であるが、数十ナノ秒程度の非常に短いパルス幅で、数十kHz程度もの高繰り返し発振するのが特徴である。発振器出口からは直径数ミリの円形ビームを出力してレンズで集光するのだが、波長が短くなると小さく集光することができるので微細孔(穴)あけに適している。ここでは、板厚0.1mmのガラスに直径2μmの微細孔(穴)あけを行ったサンプルを図8に示す。レーザ波長を選択することにより、材料に依存せずに加工できることが、ドリル加工に対するレーザ加工の利点である。前述のエキシマレーザの繰り返し周波数は数百Hzであるのに対し、半導体励起固体レーザでは数十kHzでおよそ2ケタ違うため、1ショットあたりのパルスエネルギーが小さい。少しずつ除去して熱を加え過ぎないように配慮する必要がある。
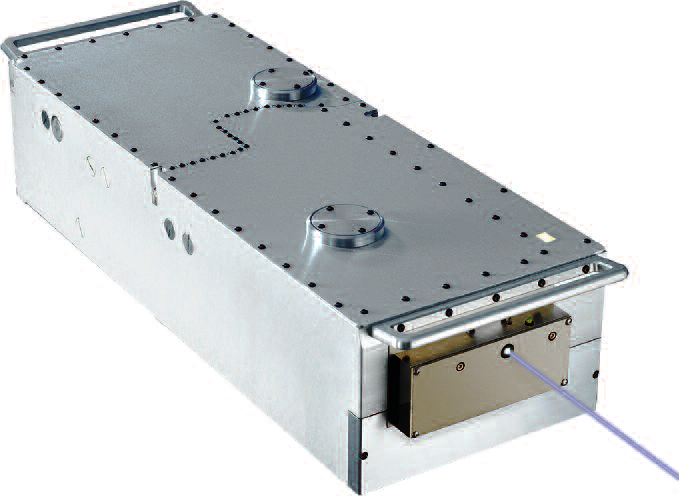
図7 半導体励起固体レーザ(3倍高調波)の一例(スペクトラ・フィジックス社カタログより)
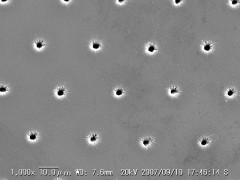
図8 半導体励起固体レーザ(4倍高調波)によるガラス孔(穴)あけサンプル(弊社加工事例より)
6.パルスファイバーレーザによる金属孔(穴)あけ
近年注目されているレーザ発振器の一つに、ファイバーレーザがある。高出力で高ビーム品質なので、連続発振タイプのファイバーレーザでは高いエネルギー密度を利用した金属などの溶接、切断に使われてきた。ここでは孔(穴)あけ用途として注目しているパルスファイバーレーザについて取り上げる。弊社では、図9に示すように非常にコンパクトな筺体から、パルスエネルギー1mJ、パルス幅50ns、周波数30~80kHzを発振する発振器を所有している。これにガルバノ加工機を組み合わせ、薄板に大量の孔(穴)加工を行うことができる。ガルバノ加工機とは、図10に示すように2枚のガルバノミラーを高速で振ることにより高速加工ができるものである。図11にパルスファイバーレーザによる金属孔(穴)あけサンプルを示す。板厚76μmのアルミニウム合金A3003に300穴/秒もの高速で直径30μm、孔(穴)ピッチ0.1mmの微細孔(穴)加工を行っている。ここまでの高速で孔(穴)あけを行うには、孔径がビーム径と同等の必要があるので、成立条件が限定されてしまうが、ドリル加工では実現不可能な高速性が特徴である。ガルバノ加工機は、ここで取り上げたパルスファイバーレーザのほか、前述した半導体励起固体レーザなどの高繰り返しパルス発振レーザと組み合わせることにより、孔(穴)あけや溝加工に利用されている。
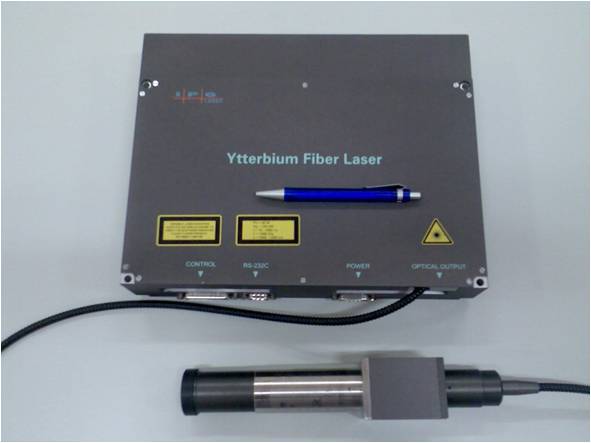
図9 パルスファイバーレーザ(弊社加工機より)
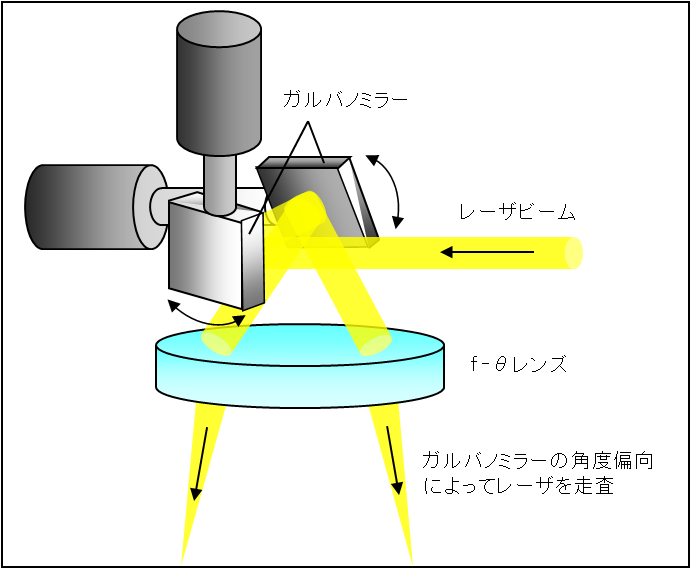
図10 ガルバノ加工機の概略図(著者自作)
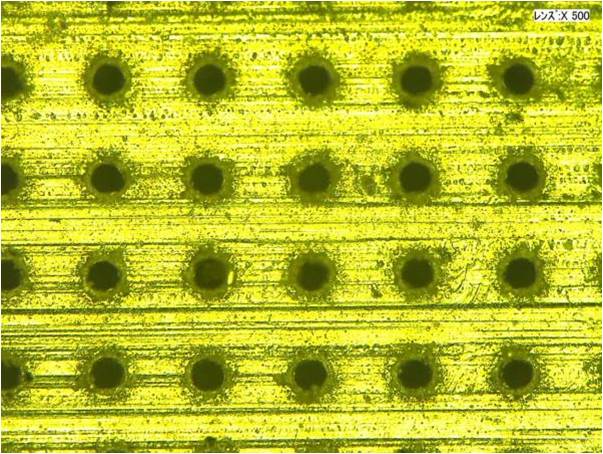
図11 パルスファイバーレーザ金属孔(穴)あけサンプル(弊社加工事例より)
7.おわりに
ドリル加工と比較しながらレーザ孔(穴)あけの特徴をレーザの種類別に紹介してきた。普段からレーザ加工を取り扱っているのでレーザ孔(穴)あけの利点を述べたつもりではあるが、逆説的にとらえればレーザ加工の限界も読み取ることができたのではないか、とも考えている。その一例として、ここでは様々なレーザ発振器が登場したように、一つのレーザ発振器で何でもできる万能なものは存在しないので、材料に応じた最適なレーザ発振器の選定が重要なのである。またこのことは、孔(穴)あけ以外の溶接や切断などのレーザ加工全般に関連している。
購読者の方々には、レーザを用いることのメリットを、まずはここで述べた孔(穴)あけを通じて感じていただき、孔(穴)あけ以外の加工方法でも積極的に利用が進んでいけば幸いである。
レーザ加工の事ならおまかせ!
本サイト運営会社レーザックスの紹介はこちら!
運営会社紹介ページへ
レーザに関する情報が盛りだくさん!
レーザ加工なびTOPへ
「レーザ孔(穴)あけの特徴 ~材料に応じた最適なレーザ発振器の選定~」
株式会社レーザックス 池田 剛司
1.はじめに
本誌の購読者はツールを使ったドリル加工による孔(穴)あけの知識や経験が豊富にあると思われるが、レーザ孔(穴)あけについてはどのようなイメージをお持ちであろうか。ツールの代わりにレーザ光を用いるというように置き換えれば簡単なのだが、光は質量を持たず空間を自由に行き来するし、多くの場合は目に見えない不可視光なので、想像しにくいと思われているかもしれない。ここでは、レーザ孔(穴)あけの加工方法と特徴を、レーザの種類別に説明するので、レーザを用いることのメリットを理解して頂ければ幸いである。
2.レーザ孔(穴)あけの特徴
レーザは光なので、ドリル加工などのような接触加工ではなく、非接触加工である。そのため、ワーク形状がレーザ入射方向に対して斜めであっても、曲面であっても加工でき、ワーク形状にあまり左右されない。この特徴を示す例として、三次元加工に対応したNd:YAGレーザ加工機で板厚2mmのステンレス鋼SUS304に様々な角度で加工した斜め孔(穴)あけサンプルを図1に示す。ドリル加工では斜めにツールを当てるとワーク表面に沿って逃げていくのだが、レーザでは照射した場所と方向そのままの孔(穴)が開くのである。
次の特徴は、加工対象材料が多いことである。セラミックスやガラスなどの硬くて脆い材料であっても、軟質ゴムなどの軟らかい材料であっても加工できる。ただし、材料に応じてレーザの波長を使い分ける必要がある。例えば定点でレーザを照射するシングルショットやパーカッションなどの微細な孔(穴)あけの場合、金属ならNd:YAGレーザ(波長1064nm)やファイバーレーザ(波長1070nm)、樹脂ならKrFエキシマレーザ(波長248nm)など、ガラスなら半導体励起固体レーザ(Nd:YAGレーザ等の4倍高調波で波長266nm)などがそれぞれ適切である。また、前述のレーザに加えてCO2レーザ(波長10.6μm)も候補に挙がる。
ここで、レーザ孔(穴)あけの加工方法を図2の模式図を用いて説明する。シングルショット及びパーカッションとは、定点でレーザを照射させる加工方法であるが、シングルショットはその名前が示す通り1ショットで孔(穴)あけを行う加工方法、パーカッションは複数ショットで孔(穴)あけを行う方法である。シングルショットでは短時間で孔(穴)あけできるが板厚に制約が出る一方、パーカッションは厚板の貫通孔(穴)加工で用いられる。いずれもビーム品質がそのまま影響し、ビーム径付近の直径しか加工できない。トレパニングは開けたい孔(穴)の輪郭に沿ってレーザ照射する加工方法であるため、様々な穴径や形状が加工でき、孔(穴)の位置形状の安定性の面で優れている。何周も走査することによって厚板加工が可能だが、微細孔(穴)では孔(穴)形状が崩れることもある。また、トレパニングを一筆書きのように一回の走査で連続して行うのがレーザ切断加工である。
そして最後に、加工速度を特徴として挙げる。レーザはレンズなどによって集光させることにより、高いエネルギーを小さな面積に集中させる。これにより材料の溶融・蒸発除去が爆発的に行われるため、他の加工方法に比べて加工速度が速いのである。表1に、タービンブレードへの冷却孔(穴)あけを想定し、ある条件で耐熱合金ハステロイの孔(穴)あけ加工速度を比較した例を示す。パンチングが微細孔(穴)あけに向かないこと、電子ビームが真空中で行うこと、これらを除けばレーザの孔(穴)あけ加工速度が最も速い。
以上のような特徴を持つレーザ孔(穴)あけであるが、次項からはレーザの種類別に具体例を挙げながら特徴を説明していく。
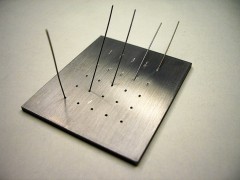
図1 Nd:YAGレーザ斜め孔(穴)あけサンプル(弊社加工事例より)
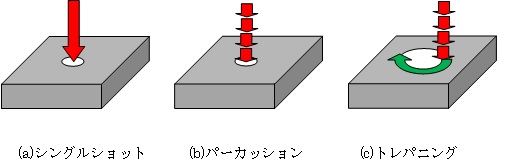
図2 レーザ孔(穴)あけ方法の模式図(著者自作)
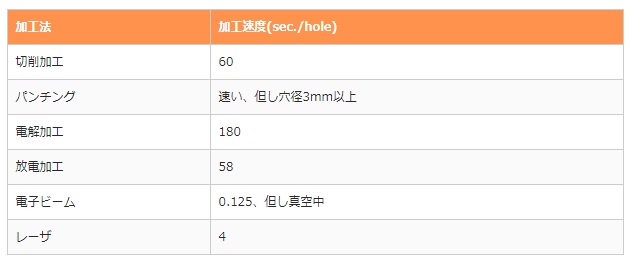
表1 ハステロイの孔(穴)あけ加工速度比較例
(高原ら、レーザによる冷却通路孔の加工技術、日本ガスタービン学会誌Vol.22 No.85 p83-89より)
3.Nd:YAGレーザによる金属孔(穴)あけ
Nd:YAGレーザでは図1に示したように金属材料に斜め孔(穴)あけが可能で、レンズを用いてレーザ光を集光することによりエネルギー密度を高くし、定点で照射するパーカッション加工により、細くて深い貫通孔(穴)加工を行う。直径0.5mm程度以下の孔(穴)あけを例にすると、鉄鋼材料では板厚25mm、アルミニウム合金や銅合金などレーザの反射が強い材料では板厚10mm、アルミナなどのセラミックスでも板厚10mmの加工事例がある。孔(穴)あけに用いられるNd:YAGレーザは、平均出力は数十~数百Wであるが、ミリ秒程度のパルス発振をさせて数十kW程度もの鋭いピーク出力を発振して材料を瞬時に溶融させる。しかし、この加工は純粋なレーザの力だけで成り立つものではない。加工機先端の、図3に示すようなアシストガスノズルから高圧のガスを吹き付けながらレーザ照射することにより溶融した金属を押し出して除去する。弊社ではアシストガスノズルの角度を変えながら加工できる三次元加工機により、航空機ジェットエンジン部品の冷却孔(穴)あけを行っている。また、別の加工機で図4に示すように直径3mmのステンレス鋼SUS304パイプに狭ピッチで直径0.5mmの孔(穴)あけを行った例を紹介する。このような加工事例を活かして医療機器のステントが製作されている。ドリル加工とは異なり、レーザは加工時に材料に力が加わらないので、このような繊細な加工が可能である。
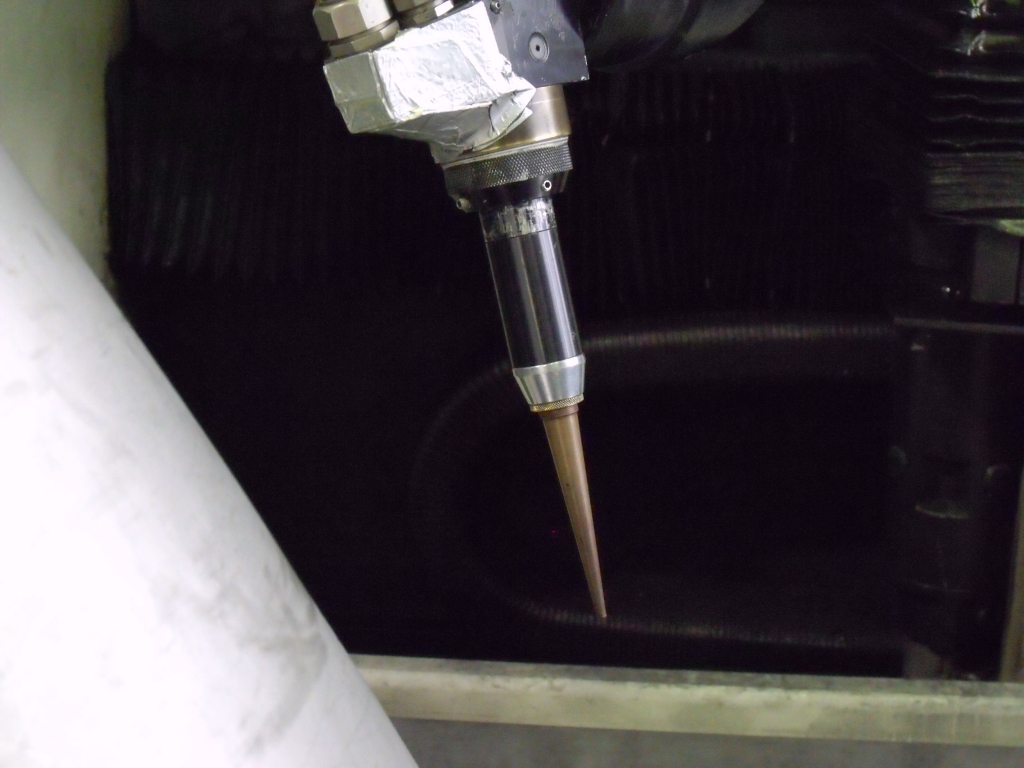
3図3 Nd:YAGレーザ加工機先端のアシストガスノズル(弊社加工機より)
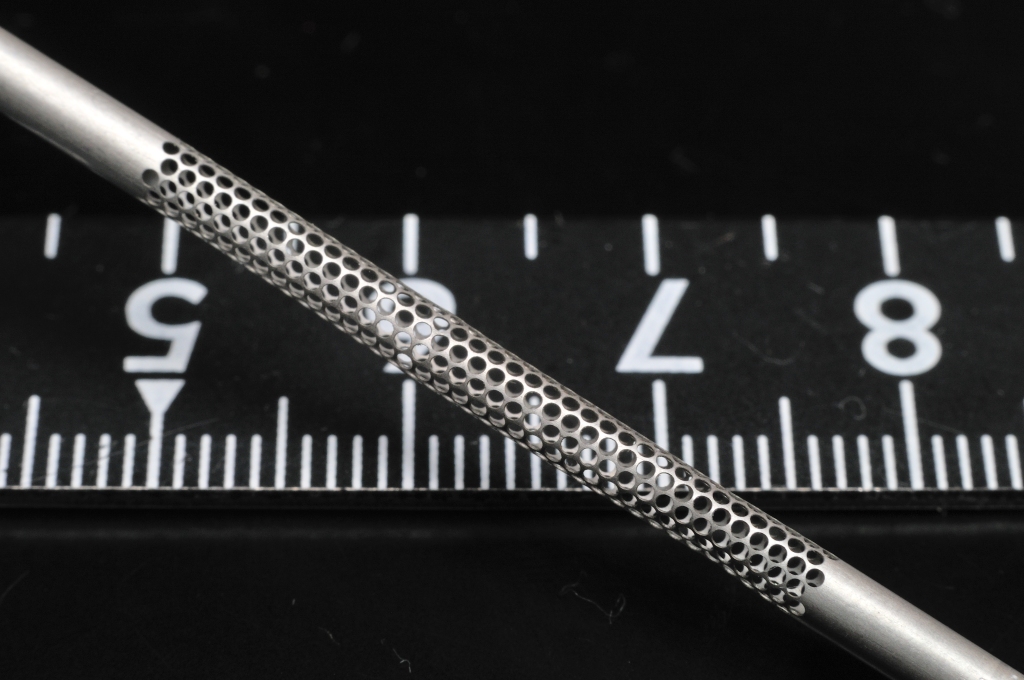
図4 Nd:YAGレーザパイプ孔(穴)あけサンプル(弊社加工事例より)
4.エキシマレーザによる樹脂孔(穴)あけ
エキシマレーザは、例えばKrFでは248nmの波長で発振するように紫外線領域の短波長であることと、数十ナノ秒という非常に短いパルス発振をさせるという特徴を持ったレーザである。波長が短ければ短いほど一般的には材料へのレーザ吸収率が高まり、効率的に熱が伝わる。また、ナノ秒という一瞬では、熱が周囲に伝わる前にレーザ照射が終了してしまうため、孔(穴)周辺の熱影響や損傷を小さくすることができる。特に樹脂材料では、金属に比べて低い温度で溶融、分解するので、一瞬にして蒸発除去される。エキシマレーザはマスク転写方式により照射するため、前述のNd:YAGレーザとは全く加工方法が異なる。その概略図を図5に示す。レンズはレーザ光を集光させるために用いるのではなく、マスク像を転写させるために用いる。図中では、レンズの焦点距離をfとして、1/A+1/B=1/f及び、A/B=L1/L2=M(=縮小率)が成立する。つまり、マスク寸法の1/Mに縮小された像がワーク上に転写される。この特徴を活かした加工事例を図6に示す。直径1.5mmのナイロン系樹脂パイプに四角形の孔(穴)を開けている。前述するようなNd:YAGレーザでは円形ビームを集光させているので円形の孔(穴)しか開けることができないが、エキシマレーザでは様々な形状の孔(穴)加工が可能である。また、円形の孔(穴)しか開けることができないドリル加工に対しても優位性がある。さらには、マスクの中に複数個の孔(穴)を開けることにより、同時多孔加工が可能なので、生産性向上につながっている事例もある。
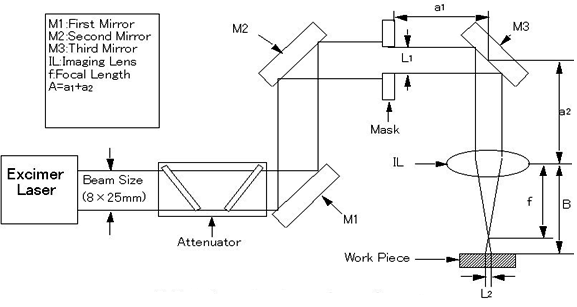
図5 エキシマレーザ加工機の概略図(著者自作)
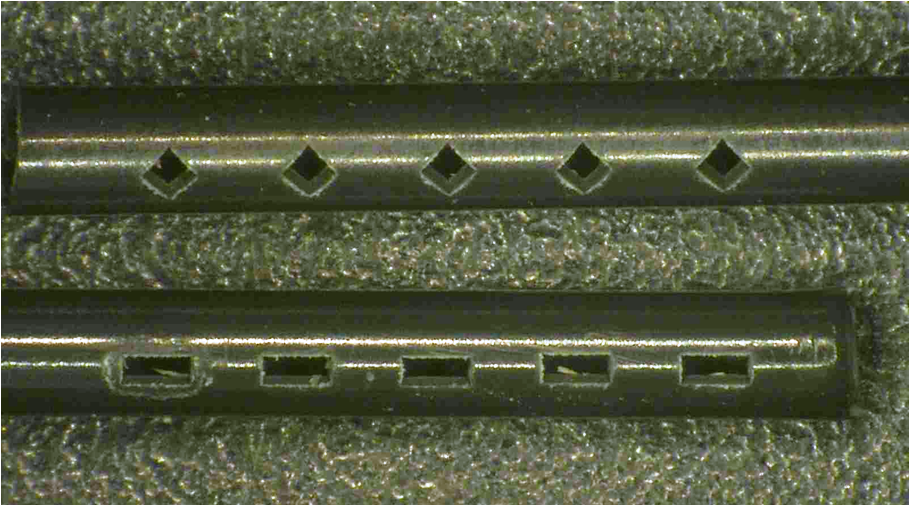
図6 エキシマレーザ樹脂パイプ孔(穴)あけサンプル(弊社加工事例より)
5.半導体励起固体レーザによるガラス孔(穴)あけ
半導体励起固体レーザは、Nd:YAGレーザ(波長1064nm)等の光が波長変換素子を経由することにより、波長532nmの2倍高調波、波長355nmの3倍高調波、及び波長266nmの4倍高調波へと波長を変換させて用いることが特徴である。その一例として、スペクトラ・フィジックス社の3倍高調波発振器を図7に示す。また、同社ではユーザ側で波長変換素子を交換可能な発振器もあるので、材料によって適した波長を適宜選択することが可能である。半導体励起固体レーザは、短波長になるほど平均出力が下がり、高くても数十W程度の平均出力であるが、数十ナノ秒程度の非常に短いパルス幅で、数十kHz程度もの高繰り返し発振するのが特徴である。発振器出口からは直径数ミリの円形ビームを出力してレンズで集光するのだが、波長が短くなると小さく集光することができるので微細孔(穴)あけに適している。ここでは、板厚0.1mmのガラスに直径2μmの微細孔(穴)あけを行ったサンプルを図8に示す。レーザ波長を選択することにより、材料に依存せずに加工できることが、ドリル加工に対するレーザ加工の利点である。前述のエキシマレーザの繰り返し周波数は数百Hzであるのに対し、半導体励起固体レーザでは数十kHzでおよそ2ケタ違うため、1ショットあたりのパルスエネルギーが小さい。少しずつ除去して熱を加え過ぎないように配慮する必要がある。
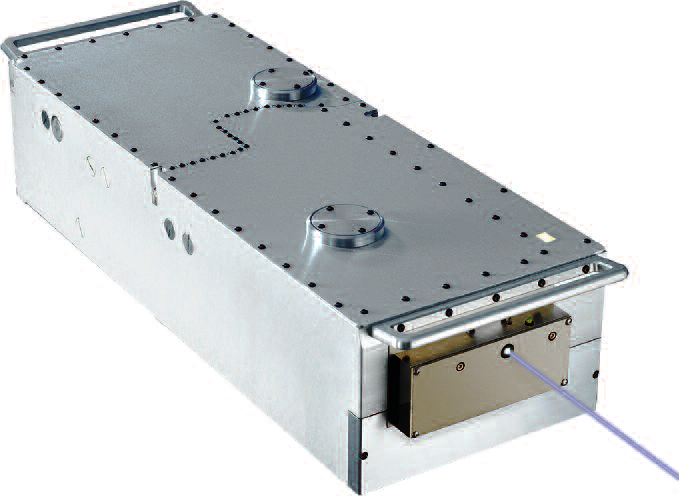
図7 半導体励起固体レーザ(3倍高調波)の一例(スペクトラ・フィジックス社カタログより)
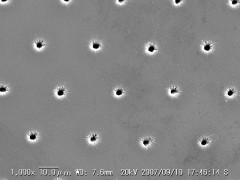
図8 半導体励起固体レーザ(4倍高調波)によるガラス孔(穴)あけサンプル(弊社加工事例より)
6.パルスファイバーレーザによる金属孔(穴)あけ
近年注目されているレーザ発振器の一つに、ファイバーレーザがある。高出力で高ビーム品質なので、連続発振タイプのファイバーレーザでは高いエネルギー密度を利用した金属などの溶接、切断に使われてきた。ここでは孔(穴)あけ用途として注目しているパルスファイバーレーザについて取り上げる。弊社では、図9に示すように非常にコンパクトな筺体から、パルスエネルギー1mJ、パルス幅50ns、周波数30~80kHzを発振する発振器を所有している。これにガルバノ加工機を組み合わせ、薄板に大量の孔(穴)加工を行うことができる。ガルバノ加工機とは、図10に示すように2枚のガルバノミラーを高速で振ることにより高速加工ができるものである。図11にパルスファイバーレーザによる金属孔(穴)あけサンプルを示す。板厚76μmのアルミニウム合金A3003に300穴/秒もの高速で直径30μm、孔(穴)ピッチ0.1mmの微細孔(穴)加工を行っている。ここまでの高速で孔(穴)あけを行うには、孔径がビーム径と同等の必要があるので、成立条件が限定されてしまうが、ドリル加工では実現不可能な高速性が特徴である。ガルバノ加工機は、ここで取り上げたパルスファイバーレーザのほか、前述した半導体励起固体レーザなどの高繰り返しパルス発振レーザと組み合わせることにより、孔(穴)あけや溝加工に利用されている。
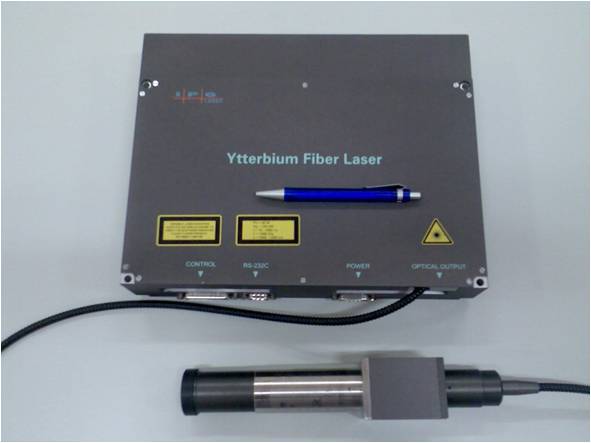
図9 パルスファイバーレーザ(弊社加工機より)
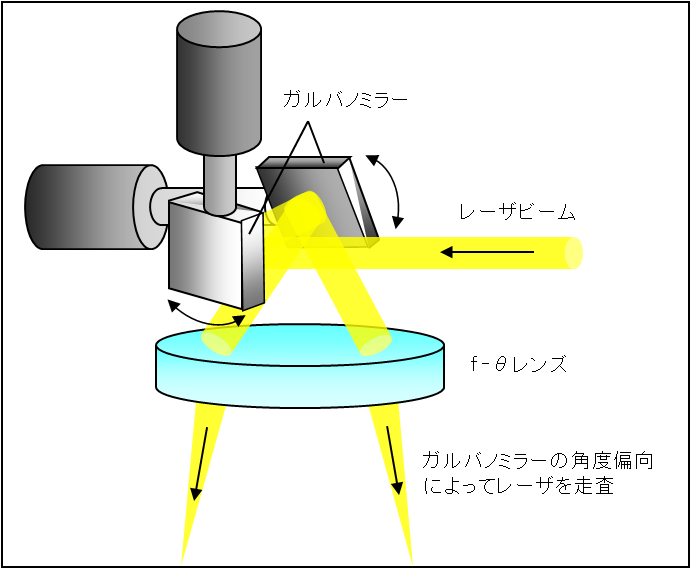
図10 ガルバノ加工機の概略図(著者自作)
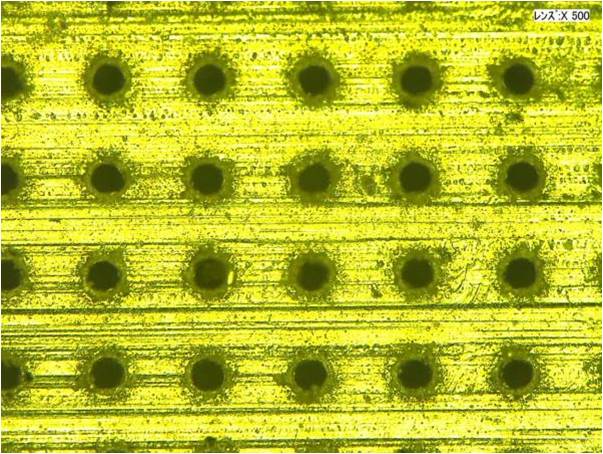
図11 パルスファイバーレーザ金属孔(穴)あけサンプル(弊社加工事例より)
7.おわりに
ドリル加工と比較しながらレーザ孔(穴)あけの特徴をレーザの種類別に紹介してきた。普段からレーザ加工を取り扱っているのでレーザ孔(穴)あけの利点を述べたつもりではあるが、逆説的にとらえればレーザ加工の限界も読み取ることができたのではないか、とも考えている。その一例として、ここでは様々なレーザ発振器が登場したように、一つのレーザ発振器で何でもできる万能なものは存在しないので、材料に応じた最適なレーザ発振器の選定が重要なのである。またこのことは、孔(穴)あけ以外の溶接や切断などのレーザ加工全般に関連している。
購読者の方々には、レーザを用いることのメリットを、まずはここで述べた孔(穴)あけを通じて感じていただき、孔(穴)あけ以外の加工方法でも積極的に利用が進んでいけば幸いである。
レーザ加工の事ならおまかせ!
本サイト運営会社レーザックスの紹介はこちら!
運営会社紹介ページへ
レーザに関する情報が盛りだくさん!
レーザ加工なびTOPへ