ファイバーレーザによる精密加工
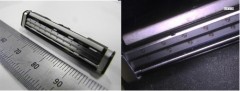
「溶接技術」 2013年5月号より
ファイバーレーザによる精密加工
株式会社レーザックス 羽田 光明
1 はじめに
ファイバーレーザが登場する前に、Nd:YAGレーザの適用拡大の中で、ニ、三の先進的な出来事があった。一つは、レーザ溶接が身近なものに適用され、生産のために多数のパルスNd:YAG発振器が導入された事である。写真1は当時のカミソリ刃(razor)である。写真2は使用しなくなったノートパソコンのハードディスクから取出したヘッド先端部で、10ヶ所程のレーザスポット溶接が認められる。いずれも高精度、低歪の組立加工法としてNd:YAGレーザ溶接が活用された例である。もう一つは、5kW級の出力が安定して得られるNd:YAGレーザ発振器が登場した事である。その後の高出力化の経過は周知のところであり、本誌でも多くの報告がある1)。本稿では、掌(手のひら)サイズをイメージした対象製品の加工を中心に、ファイバーレーザの特長である高輝度・高精細を活かした加工例を紹介する。
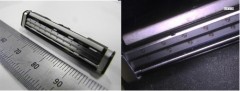
写真1 カミソリ刃
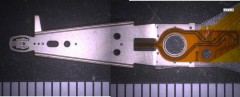
写真2 ハードディスクヘッド
2 ファイバーレーザの紹介
図1にファイバーレーザの出力推移を示す。ここ10年の高出力化は急峻であり、国内では産業用として、30kWのマルチモード発振器が稼働中である。さらに100kWの計画もある。一方、シングルモードの高出力化も急速に進み、10kW級が開発されており、国内では3kWの発振器が稼働中である。パルスファイバーレーザについても、平均パワーの推移を併記した2),3)。
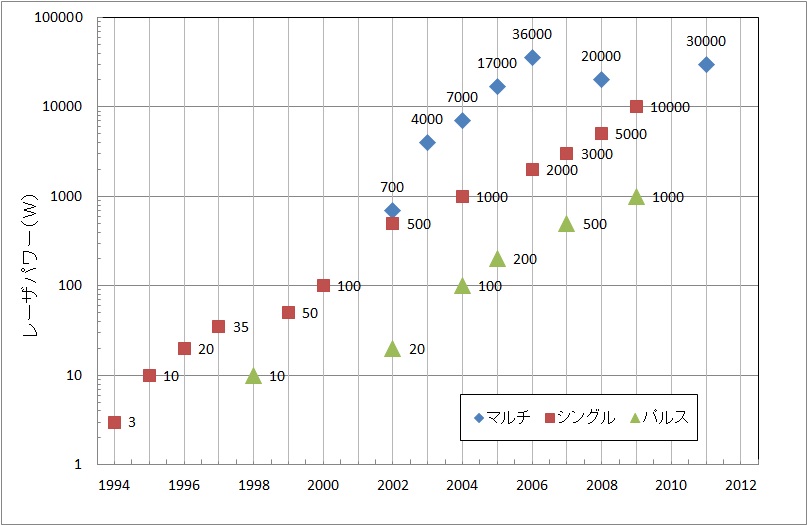
図1 ファイバーレーザの出力推移
図2に溶接、切断に使われる熱源のパワー密度の比較を示す。Nd:YAGレーザのパワー密度はアーク、プラズマ熱源の1~2桁上、ファイバーレーザはそのNd:YAGレーザの2桁上の高いパワー密度である。さらに、極細径(例:10μm)のファイバーを使用するシングルモードでは、300Wでもマルチモードの30kWを上回るパワー密度になり、従来の特性とは異なった超高速度・高精密加工への適用が期待される。
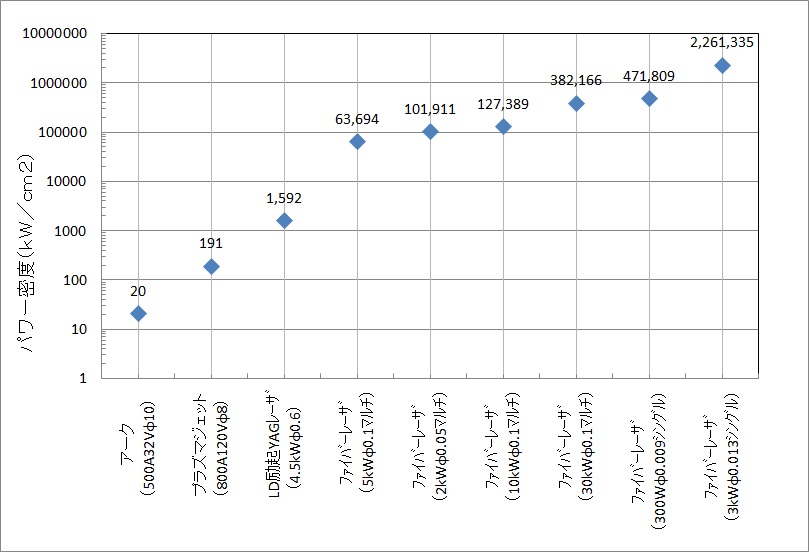
図2 加工熱源のパワー密度比較
図3にファイバーレーザのパルス出力の模式図を示す。CW発振は一定出力の連続発振レーザである。CWレーザを変調やモジュレーションと呼ばれるゲートパルス発振で断続的に出力してパルス化することができる。しかし、CW発振出力以上のピーク出力は得られない。QCW(Quasi CW)ファイバーレーザは、CW発振では得られない高ピーク出力のパルス発振が可能で、同時にCW発振モードも設定できるので幅広い加工に対応できる4)。n秒パルスファイバーレーザはパルス幅が短くピーク出力が高いので、穴(孔)明け、表面加工などの除去加工に使われる。p秒、f秒ファイバーレーザは極短パルスレーザとして注目されている5),6)。レーザ加工条件には材質によるレーザ光の吸収を考慮した波長の選択などもあるが、ここでは、従来のNd:YAGレーザの基本波と同じファイバーレーザ(例:1.07μm)による精密・微細加工を紹介する。
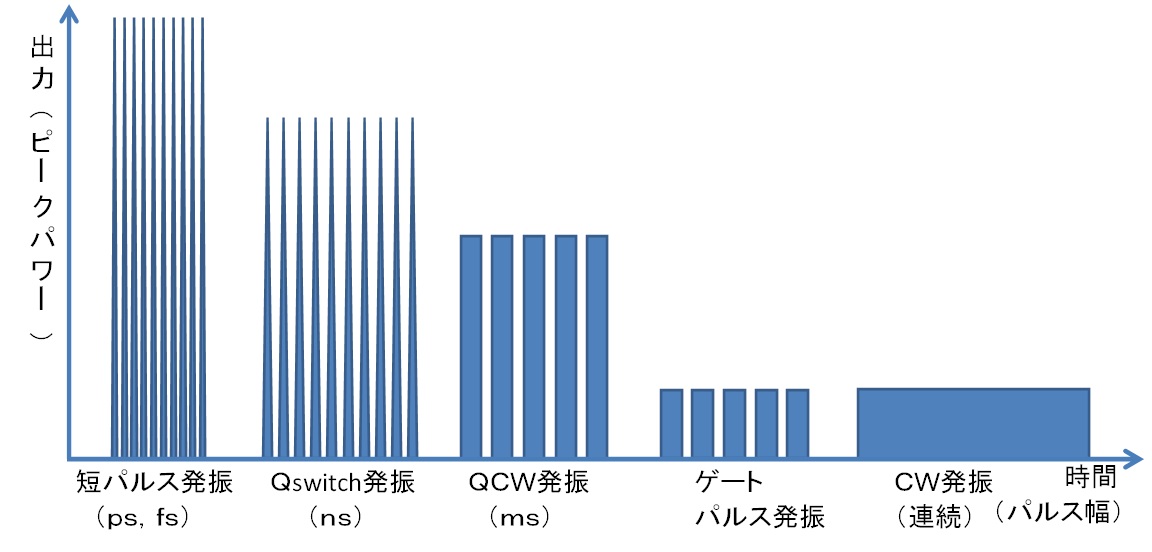
図3 パルスファイバーレーザの出力模式図
3 レーザ加工法の特徴
レーザ加工の適用例を紹介する前に、レーザ加工法の特徴を簡単に紹介する。
3.1 レーザ溶接・溶着の特徴
レーザ光はレンズなどで非常に小さく集光することができる。レーザ溶接では小さく絞ったビームスポットにエネルギーを投入するので、溶接速度が速く熱影響が少なくなり、高品質、高精度な加工ができる。写真3はパイプの狭隘部の溶接例である。パイプの外径は6mmである。パイプの間隙が狭く溶接が困難な形状でも、長焦点レンズを使用して遠くから細いビームを照射することで、パイプに干渉しない。対象材質は鉄鋼、アルミニウム、銅などの各種金属材料である。金属以外では樹脂の溶着があり、自動車部品や医療機器に適用している。
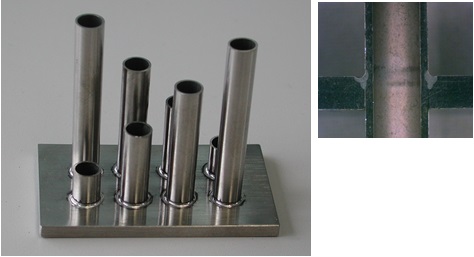
写真3 レーザ溶接の加工例(狭隘部の溶接)
3.2 レーザ切断の特徴
板金加工などの業界では、薄板から中厚板の切断をするCO2レーザが広く普及している。CO2レーザはもちろん、Nd:YAGレーザ、ファイバーレーザ切断では、溶接と同様に小さく絞ったビームスポットにエネルギーを投入するので、切断速度が速く熱影響が少なくなり、高品質、高精度な加工ができる。写真4は各種金属の切断例である。対象材質は鉄鋼、アルミニウム、銅などの金属材料から、樹脂、セラミックス、ガラス、紙や木材などの非金属、複合材料まで広範囲である。対象材質が多いことも特徴で、各種材質に適したレーザが選択される。
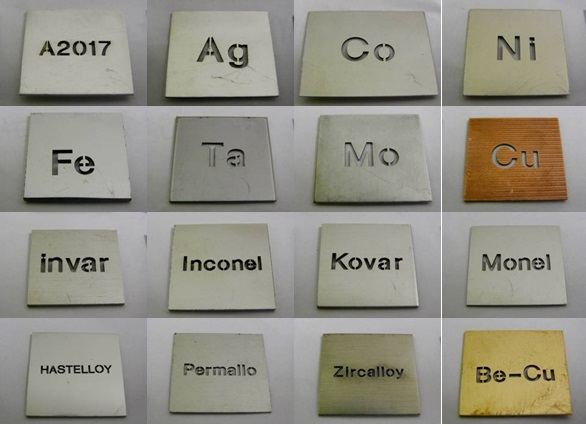
写真4 レーザ切断の加工例(各種金属の切断)
3.3 レーザ孔(穴)明けの特徴
レーザ光による孔(穴)明けは、小さなビームスポットに高いパワーを投入することで、材料の溶融・蒸発・除去が爆発的に進行するので、他の加工法に比べて加工速度が速い。また、ドリルなどの接触加工ではなく、非接触加工であるため、加工面の形状が傾斜面や曲面であっても、レーザ照射した場所に入射方向に直進する孔(穴)を明けることができる。写真5は斜め孔(穴)の加工例である。板厚6mmで、角度を示すために細線を挿入している。対象材質は、切断と同様に金属材料はもちろん、セラミックスやガラスなどの硬くて脆い材料、樹脂やゴムなどの軟らかい材料の加工も可能であり、各種材質に応じてレーザを使い分ける。
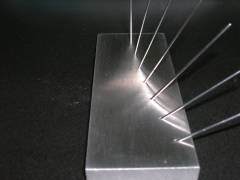
写真5 レーザ孔(穴)明けの加工例(斜め孔加工)
3.4 レーザ表面加工の特徴
スキャナ(ガルバノミラー)によりレーザ光を高速で走査して、材料表面の高品質、高精度な加工ができる。μ秒やn秒の短いパルスを発生するレーザを用いて、瞬時に材料表面を蒸発・除去することにより、微小な深さ制御が可能となり、高精度で鋭利な加工ができる。スキャナによる加工法は、表面に付着した汚れ、塗料、酸化皮膜などを除去するレーザクリーニングにも適用される。写真6は精密除去加工の加工例である。0.5mmずつ6段階の深さに加工した。
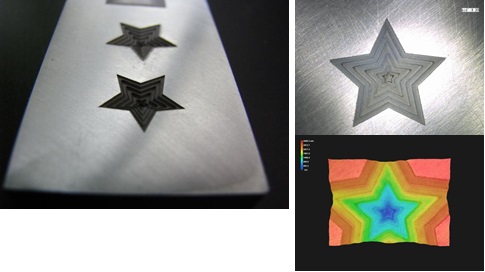
写真6 レーザ表面加工(精密除去加工)
4 レーザ加工の適用例
ファイバーレーザによる精密加工の適用例を紹介する。本稿では、製品の代わりに平板或いは展示サンプルとして製作した模擬形状の加工例を記載した。レーザ加工条件の一部を参考値として載せたが、レーザ特有の光としての条件-焦点距離、焦点位置、ビームスポット径なども必要である。さらに、精密加工の実施工においては、ガスや治具などの周辺条件が重要な要素となる。
4.1 マルチモードファイバーレーザの加工例
2kW級のマルチモードファイバーレーザによる加工例を紹介する。
(1)溶接、溶着
写真3もマルチモードレーザの加工例である。写真7は熱交換器を模擬したチューブと管板の溶接である。チューブの端面の形状を維持したまま溶接することもできる。
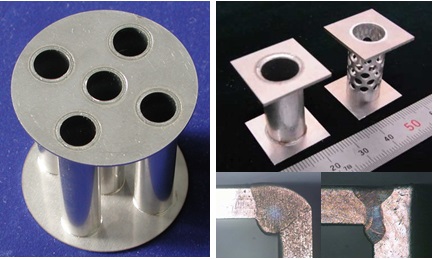
写真7 チューブの溶接
写真8は薄板の重ね溶接である。アルミニウム合金(0.3mm)を20m/minの高速で溶接した。
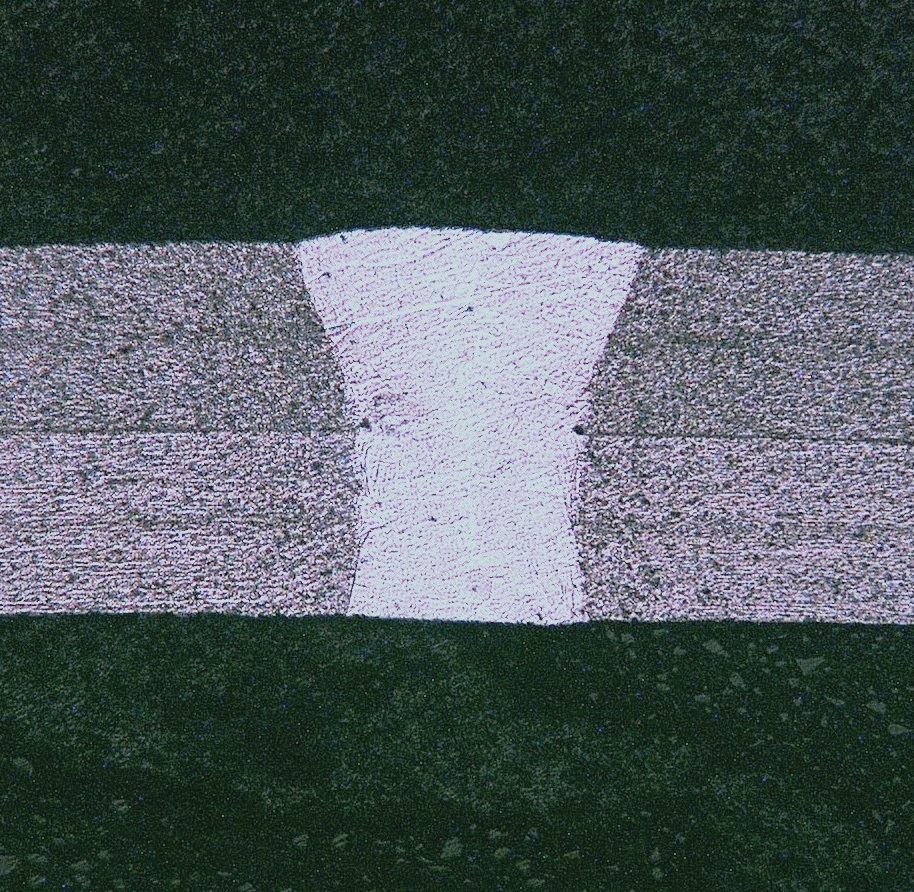
写真8 薄板の重ね溶接
写真9は異種金属の溶接である。アーク溶接が困難である黄銅(0.7mm)をステンレス鋼(1mm)に2m/minで重ね隅肉溶接をした。
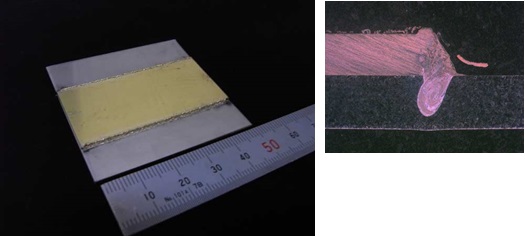
写真9 異種金属の溶接
写真10は金属と樹脂の接合である。ステンレス鋼(2mm)とナイロン(3mm)を1m/minで接合した。ステンレス鋼側からレーザを照射して加熱し、その熱によって溶融した界面のナイロンが溶着した。自動車などの輸送機器では車両軽量化による燃費向上が進んでおり、今後、金属と複合材料(CFRPなど)との直接接合が期待される。
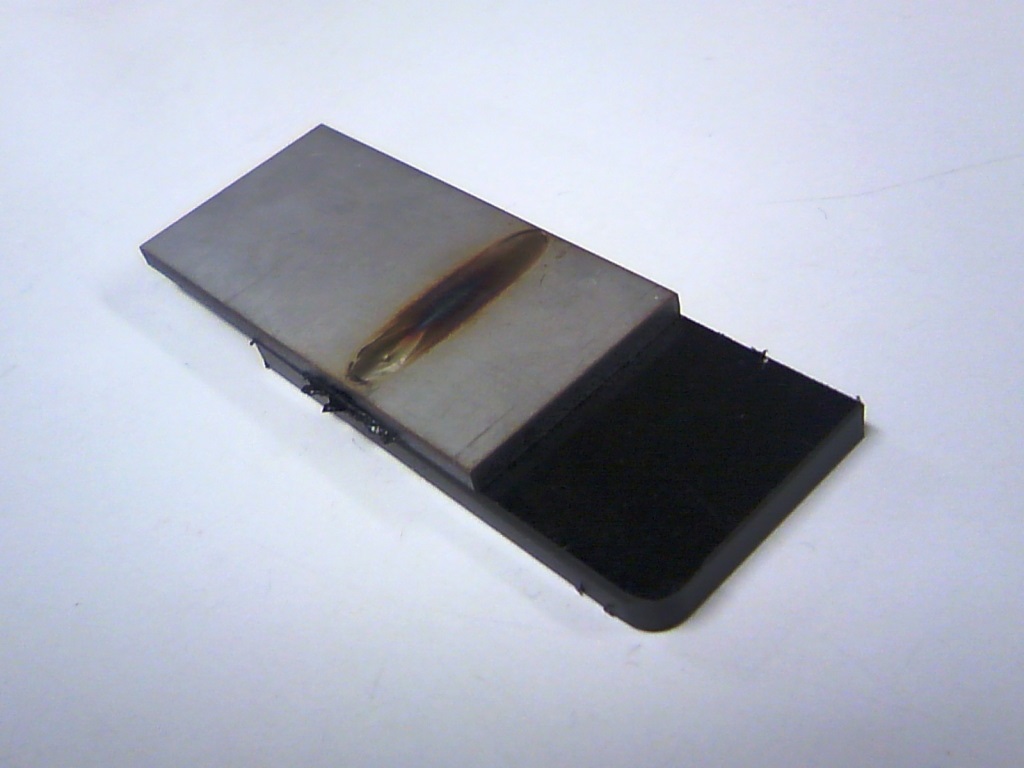
写真10 金属と樹脂の直接接合
(2)切断
写真11はパイプの切断である。アルミニウムパイプ(肉厚1mm)に2m/minで、自由な形状の切断(穴明け)をした。鉄鋼、アルミニウム、ニッケル・チタンの各合金・銅・銀などの切断ができる。また、ファイバーレーザなら、切断から溶接までを1台で加工することができる。
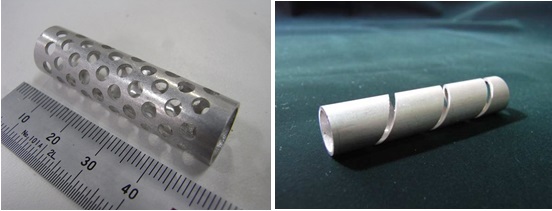
写真11 パイプの切断
(3)孔(穴)明け
写真12は孔(穴)明け加工の例である。ステンレス鋼(3mm)に、径3mm、112個の孔(穴)を明けた。加工時間は3分程度である。
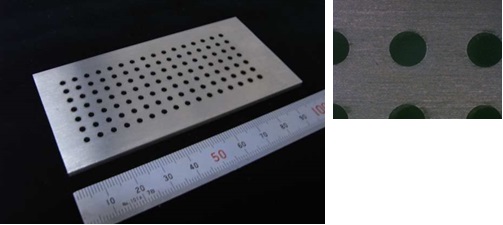
写真12 孔(穴)明け加工
4.2 シングルモードファイバーレーザの加工例
300W級のシングルモードファイバーレーザによる加工例を紹介する。
(1)溶接
写真13は薄板の重ね溶接である。燃料電池のセパレータの封止溶接を模擬したステンレス鋼(0.2mm)を30m/minの高速で溶接した。シングルモードではキーホールの径が細いので超高速溶接でもハンピングが発生しない。
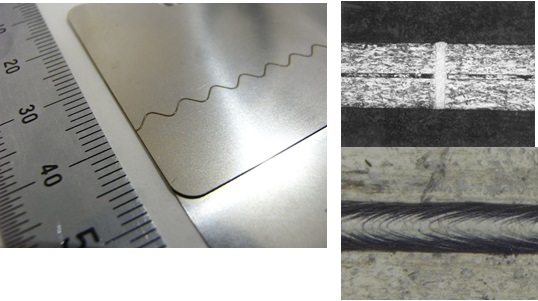
写真13 薄板の重ね溶接
写真14は薄板のヘリ継手の溶接である。ステンレス鋼(0.3mm)を8m/minで溶接した。写真15は薄板の角継手の溶接である。ステンレス鋼(0.5mm)を4m/minで溶接した。シングルモードの小さなビームスポットで高速溶接することにより、角部が溶融しない溶接ができる。
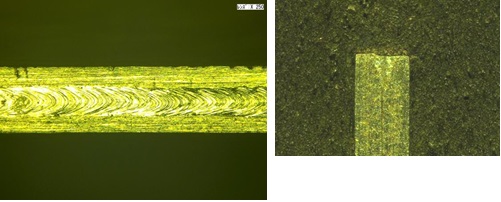
写真14 薄板のヘリ継手の溶接
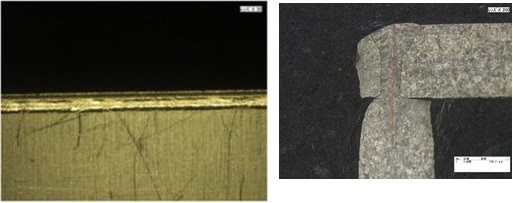
写真15 薄板の角継手の溶接
写真16は異種金属の重ね溶接である。アルミニウム(0.3mm)と銅(0.5mm)を2m/minで溶接した。高反射材の組み合わせであるが、シングルモードでビームスポットを約10μmに集光し、アルミニウム側からレーザを照射して接合した。
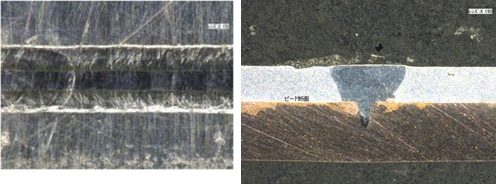
写真16 異種金属の重ね溶接
(2)切断
写真17はパイプの微細切断である。ステンレス鋼パイプ(外径6mm)を、高精度で鋭利な形状に切断した。
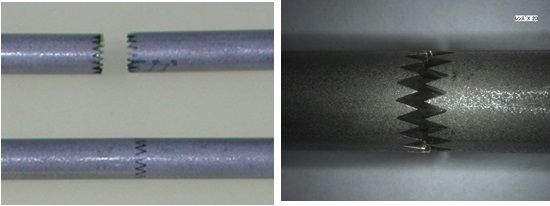
写真17 パイプの切断
写真18は細径チューブの切断である。ステンレス鋼チューブ(外径1.8mm)を部分的に微細切断して、フレキシブルチューブを製作した。
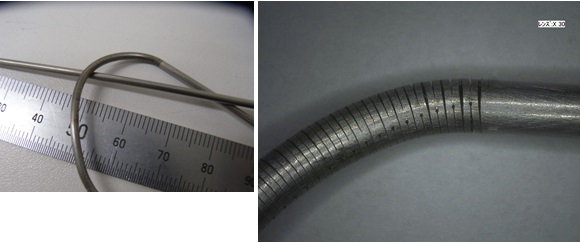
写真18 細径チューブの切断
写真19は薄鋼板の切断である。モータの電磁鋼板を模擬した鋼板(0.15mm)を30m/minで切断した。精細な切断形状の品質を確保するために、加工ステージの移動速度に同期したパルス制御によりレーザを照射した。
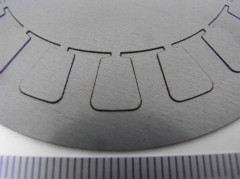
写真19 薄鋼板の切断
(3)孔(穴)明け
写真20は孔(穴)明け加工の例である。ステンレス鋼(1mm)に明けた径290,540,1015μmの孔(穴)形状である。
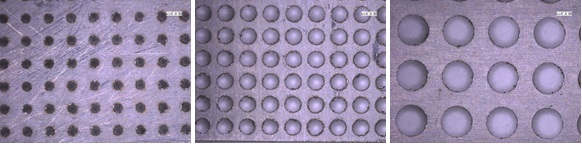
写真20 孔(穴)明け加工
(4)表面加工
「Laser Surfi-Sculpt®」加工法を紹介する。TWI(The Welding Institute)で開発され、電子ビームからレーザに発展した突起形成法である。図4に装置構成を示す。シングルモードファイバーレーザとビームスキャナーで構成される。樹脂と金属の接着強度、熱流体特性の向上などを目的に適用される7)。金属、セラミックスなどに高さ1mmを超える突起が形成できる。
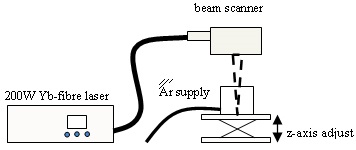
図4 装置構成
写真21は「Laser Surfi-Sculpt®」の加工例である。アルミニウム丸棒に高さ約2mmの突起が形成された。
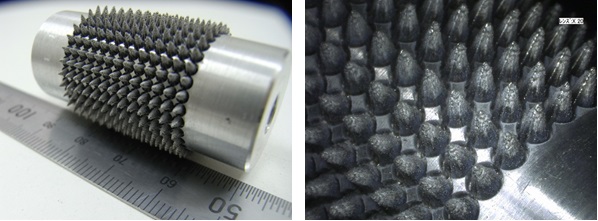
写真21 「Laser Surfi-Sculpt®」加工法
4.3 QCWファイバーレーザの加工例
平均出力150W級のQCWファイバーレーザによる加工例を紹介する。QCWレーザは高ピーク出力(例えば平均出力の10倍)のパルス発振が可能である。同時にCW発振の設定もあるので、幅広い加工に対応できる。小型、空冷、メンテナンスフリーで、今後、従来のパルスNd:YAGに替わる発振器として期待される。
(1)溶接
写真22は薄板の隅肉溶接である。チタン(0.5mm)を2m/minで溶接した。低入熱で酸化もなく、歪のない溶接ができた。
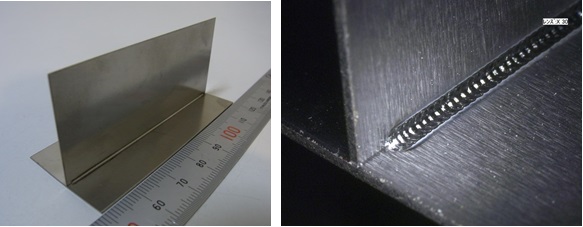
写真22 薄板の隅肉溶接 8)
(2)切断
写真4もQCWレーザの加工例である。写真23は中厚板の切断である。ステンレス鋼(5mm)を切断して、大出力レーザに比べて、高精度で鋭利な形状が得られた。
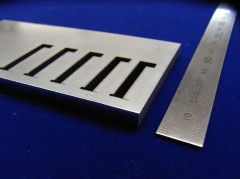
写真23 中厚板の切断
写真24は精細切断の加工例である。細いビームスポットとパルス発振による低入熱化で、0.1mmの微細なリブを製作した。
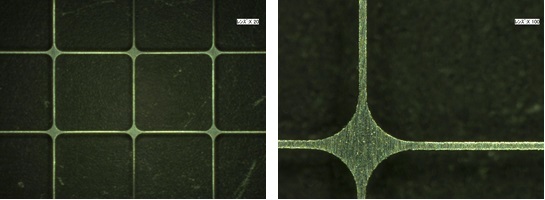
写真24 精細切断の加工例
4.4 パルスファイバーレーザの加工例
平均出力30W級のパルスファイバーレーザによる加工例を紹介する。パルスファイバーレーザは小型軽量で、パルス幅が短くピーク出力が高いので、高速穴明け、除去加工に使われる。
(1)溶接
写真25は極薄板の重ね溶接である。スキャナを用いて、チタン箔(3μm)を90m/minの高速で接合した。
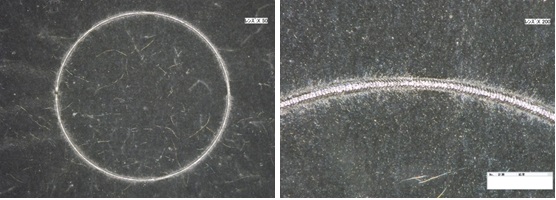
写真25 極薄板の重ね溶接
(2)孔(穴)明け
写真26は微細孔(穴)明け加工の例である。ニッケル箔(10μm)に径30μmの孔(穴)を明けた。写真27はアルミニウム箔(76μm)の場合で、入射側(左)径30μm、出射側(右)径20μmの孔(穴)が得られた。スキャナを用いてレーザ光を高速で走査することにより、良好な孔(穴)径の再現性と真円度で、300孔/杪の高速孔(穴)明け加工ができた。写真28は微細孔(穴)明け加工の応用を模擬して、アルミニウムにマーキングした例である。バックライトの透過光が確認できる。
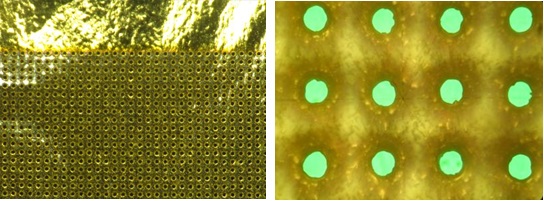
写真26 微細孔(穴)明け加工
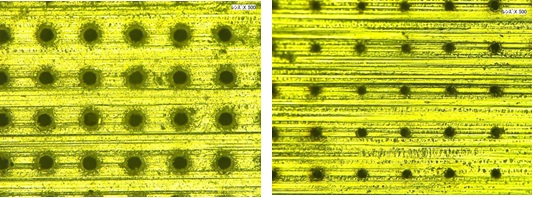
写真27 微細孔(穴)明け加工

写真28 微細孔(穴)明けの応用例
(3)表面加工
写真6もパルスファイバーレーザの加工例である。写真29は精密除去加工の例である。超硬材に溝を形成した。スキャナを用いてレーザ光を30m/minの高速で走査することにより、微小な深さ制御ができ、高精度で鋭利な加工ができた。写真30は精密除去加工の応用を模擬して、ステンレス鋼に、周囲を除去した漢字を描画した。
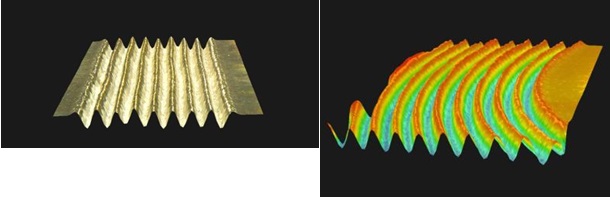
写真29 精密除去加工
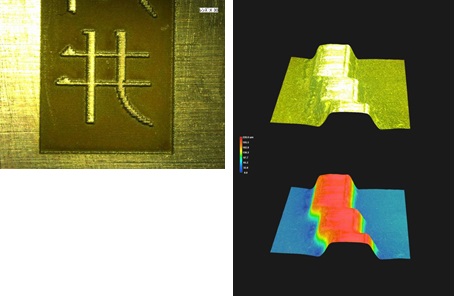
写真30 精密除去の応用例
「Clean-Lasersysteme」によるレーザクリーニングを紹介する。図5にレーザクリーニングの原理を示す。集光されたパルスレーザを除去層に吸収させ、アブレーションと呼ばれる昇華と、素材に与える微小な熱エネルギーの衝撃による表面破壊により除去加工が行われる。適用先は溶接の前洗浄、錆・酸化膜除去、接着の前処理、塗装剥離、金型の汚染物除去などである。その優位性は、乾式で薬品の副廃棄物がないこと、素材への影響の軽減、インラインでの処理などである9)。
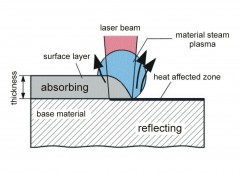
図5 レーザクリーニングの原理
写真31はレーザクリーニングの加工例である。左は鋼板上の赤錆を、右は黒色アルマイト皮膜を除去した。
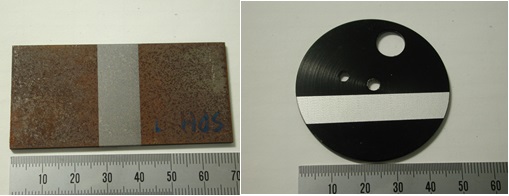
写真31 レーザクリーニング
5 おわりに
この度は精密加工の観点から、ファイバーレーザによる種々の加工例を紹介した。業界や製品別に分類することもできたが、掲載の可否などがあるので、実際に施工(試験)した加工例を発振器別に示した。その発振器も、海外だけではなく国内でも急速に開発、高性能化が進んでいる。ファイバーレーザに関して、すでに色々な誌面・講演などで報告されているが、実製品への適用についての紹介は少ないと思われるので、少しでも参考になれば幸いである。
参考文献
1) 荒谷:溶接技術, Vol.53, No.7, pp.155-160 (2005)など
2) 辻:高温学会誌, Vol.35, No.4, pp.171-175 (2009)
3) IPGフォトニクスジャパン(株):WEB資料
4) IPGフォトニクスジャパン(株):カタログ
5) 特集:OPTRONICS, No.4 (2006)
6) 特集:レーザ協会誌, Vol.28, No.2 (2003)
7) TWI:WEB資料
8) 第6回レーザー加工技術展で入手 (2013-4)
9) 本村:溶接技術, Vol.56, No.11, pp.69-71 (2008)
レーザ加工の事ならおまかせ!
本サイト運営会社レーザックスの紹介はこちら!
運営会社紹介ページへ
レーザに関する情報が盛りだくさん!
レーザ加工なびTOPへ
ファイバーレーザによる精密加工
株式会社レーザックス 羽田 光明
1 はじめに
ファイバーレーザが登場する前に、Nd:YAGレーザの適用拡大の中で、ニ、三の先進的な出来事があった。一つは、レーザ溶接が身近なものに適用され、生産のために多数のパルスNd:YAG発振器が導入された事である。写真1は当時のカミソリ刃(razor)である。写真2は使用しなくなったノートパソコンのハードディスクから取出したヘッド先端部で、10ヶ所程のレーザスポット溶接が認められる。いずれも高精度、低歪の組立加工法としてNd:YAGレーザ溶接が活用された例である。もう一つは、5kW級の出力が安定して得られるNd:YAGレーザ発振器が登場した事である。その後の高出力化の経過は周知のところであり、本誌でも多くの報告がある1)。本稿では、掌(手のひら)サイズをイメージした対象製品の加工を中心に、ファイバーレーザの特長である高輝度・高精細を活かした加工例を紹介する。
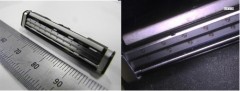
写真1 カミソリ刃
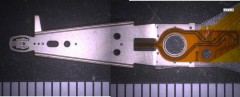
写真2 ハードディスクヘッド
2 ファイバーレーザの紹介
図1にファイバーレーザの出力推移を示す。ここ10年の高出力化は急峻であり、国内では産業用として、30kWのマルチモード発振器が稼働中である。さらに100kWの計画もある。一方、シングルモードの高出力化も急速に進み、10kW級が開発されており、国内では3kWの発振器が稼働中である。パルスファイバーレーザについても、平均パワーの推移を併記した2),3)。
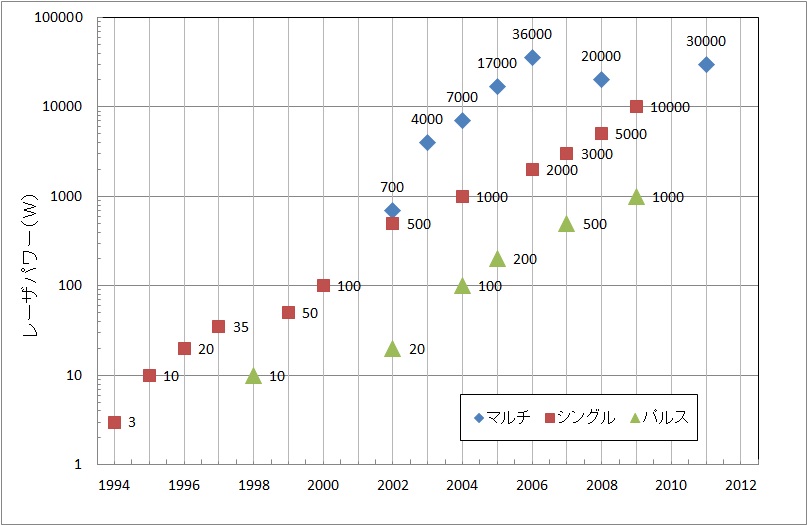
図1 ファイバーレーザの出力推移
図2に溶接、切断に使われる熱源のパワー密度の比較を示す。Nd:YAGレーザのパワー密度はアーク、プラズマ熱源の1~2桁上、ファイバーレーザはそのNd:YAGレーザの2桁上の高いパワー密度である。さらに、極細径(例:10μm)のファイバーを使用するシングルモードでは、300Wでもマルチモードの30kWを上回るパワー密度になり、従来の特性とは異なった超高速度・高精密加工への適用が期待される。
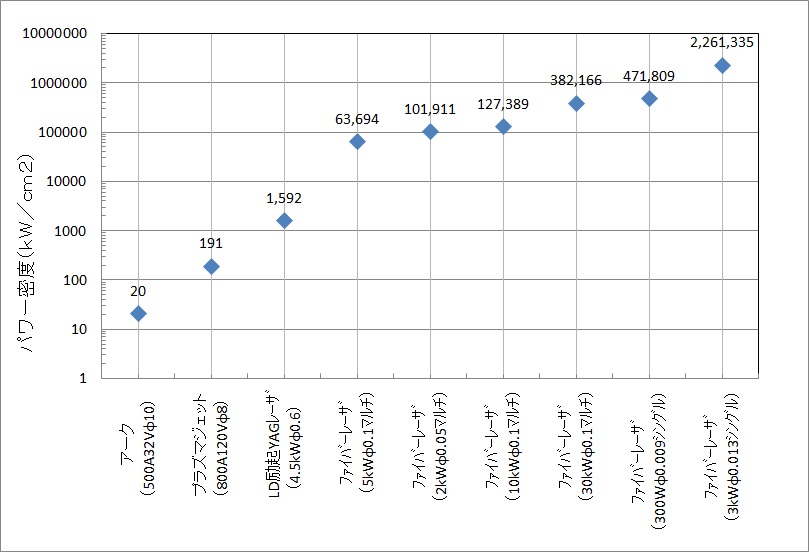
図2 加工熱源のパワー密度比較
図3にファイバーレーザのパルス出力の模式図を示す。CW発振は一定出力の連続発振レーザである。CWレーザを変調やモジュレーションと呼ばれるゲートパルス発振で断続的に出力してパルス化することができる。しかし、CW発振出力以上のピーク出力は得られない。QCW(Quasi CW)ファイバーレーザは、CW発振では得られない高ピーク出力のパルス発振が可能で、同時にCW発振モードも設定できるので幅広い加工に対応できる4)。n秒パルスファイバーレーザはパルス幅が短くピーク出力が高いので、穴(孔)明け、表面加工などの除去加工に使われる。p秒、f秒ファイバーレーザは極短パルスレーザとして注目されている5),6)。レーザ加工条件には材質によるレーザ光の吸収を考慮した波長の選択などもあるが、ここでは、従来のNd:YAGレーザの基本波と同じファイバーレーザ(例:1.07μm)による精密・微細加工を紹介する。
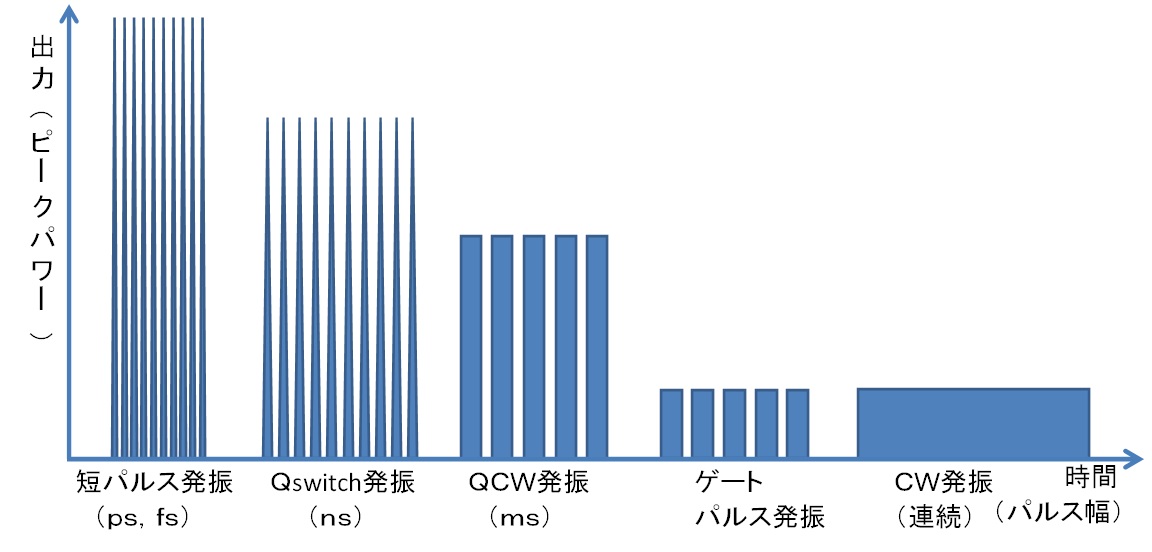
図3 パルスファイバーレーザの出力模式図
3 レーザ加工法の特徴
レーザ加工の適用例を紹介する前に、レーザ加工法の特徴を簡単に紹介する。
3.1 レーザ溶接・溶着の特徴
レーザ光はレンズなどで非常に小さく集光することができる。レーザ溶接では小さく絞ったビームスポットにエネルギーを投入するので、溶接速度が速く熱影響が少なくなり、高品質、高精度な加工ができる。写真3はパイプの狭隘部の溶接例である。パイプの外径は6mmである。パイプの間隙が狭く溶接が困難な形状でも、長焦点レンズを使用して遠くから細いビームを照射することで、パイプに干渉しない。対象材質は鉄鋼、アルミニウム、銅などの各種金属材料である。金属以外では樹脂の溶着があり、自動車部品や医療機器に適用している。
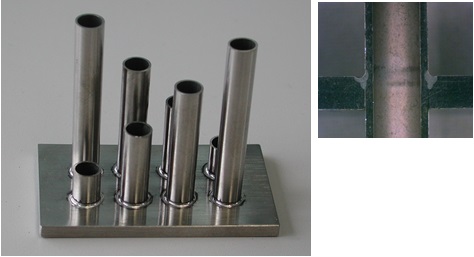
写真3 レーザ溶接の加工例(狭隘部の溶接)
3.2 レーザ切断の特徴
板金加工などの業界では、薄板から中厚板の切断をするCO2レーザが広く普及している。CO2レーザはもちろん、Nd:YAGレーザ、ファイバーレーザ切断では、溶接と同様に小さく絞ったビームスポットにエネルギーを投入するので、切断速度が速く熱影響が少なくなり、高品質、高精度な加工ができる。写真4は各種金属の切断例である。対象材質は鉄鋼、アルミニウム、銅などの金属材料から、樹脂、セラミックス、ガラス、紙や木材などの非金属、複合材料まで広範囲である。対象材質が多いことも特徴で、各種材質に適したレーザが選択される。
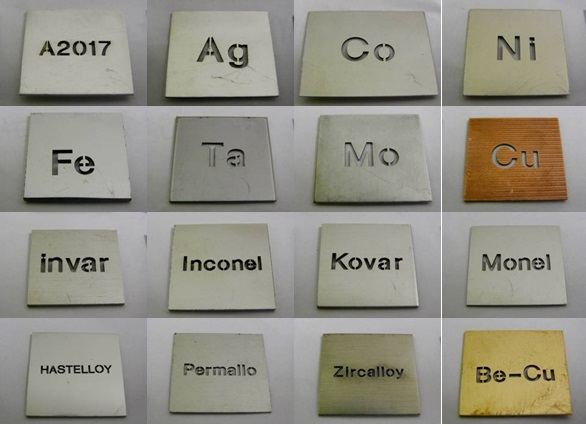
写真4 レーザ切断の加工例(各種金属の切断)
3.3 レーザ孔(穴)明けの特徴
レーザ光による孔(穴)明けは、小さなビームスポットに高いパワーを投入することで、材料の溶融・蒸発・除去が爆発的に進行するので、他の加工法に比べて加工速度が速い。また、ドリルなどの接触加工ではなく、非接触加工であるため、加工面の形状が傾斜面や曲面であっても、レーザ照射した場所に入射方向に直進する孔(穴)を明けることができる。写真5は斜め孔(穴)の加工例である。板厚6mmで、角度を示すために細線を挿入している。対象材質は、切断と同様に金属材料はもちろん、セラミックスやガラスなどの硬くて脆い材料、樹脂やゴムなどの軟らかい材料の加工も可能であり、各種材質に応じてレーザを使い分ける。
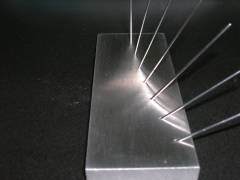
写真5 レーザ孔(穴)明けの加工例(斜め孔加工)
3.4 レーザ表面加工の特徴
スキャナ(ガルバノミラー)によりレーザ光を高速で走査して、材料表面の高品質、高精度な加工ができる。μ秒やn秒の短いパルスを発生するレーザを用いて、瞬時に材料表面を蒸発・除去することにより、微小な深さ制御が可能となり、高精度で鋭利な加工ができる。スキャナによる加工法は、表面に付着した汚れ、塗料、酸化皮膜などを除去するレーザクリーニングにも適用される。写真6は精密除去加工の加工例である。0.5mmずつ6段階の深さに加工した。
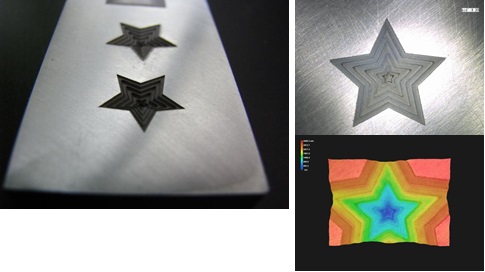
写真6 レーザ表面加工(精密除去加工)
4 レーザ加工の適用例
ファイバーレーザによる精密加工の適用例を紹介する。本稿では、製品の代わりに平板或いは展示サンプルとして製作した模擬形状の加工例を記載した。レーザ加工条件の一部を参考値として載せたが、レーザ特有の光としての条件-焦点距離、焦点位置、ビームスポット径なども必要である。さらに、精密加工の実施工においては、ガスや治具などの周辺条件が重要な要素となる。
4.1 マルチモードファイバーレーザの加工例
2kW級のマルチモードファイバーレーザによる加工例を紹介する。
(1)溶接、溶着
写真3もマルチモードレーザの加工例である。写真7は熱交換器を模擬したチューブと管板の溶接である。チューブの端面の形状を維持したまま溶接することもできる。
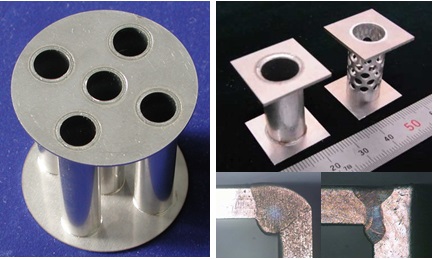
写真7 チューブの溶接
写真8は薄板の重ね溶接である。アルミニウム合金(0.3mm)を20m/minの高速で溶接した。
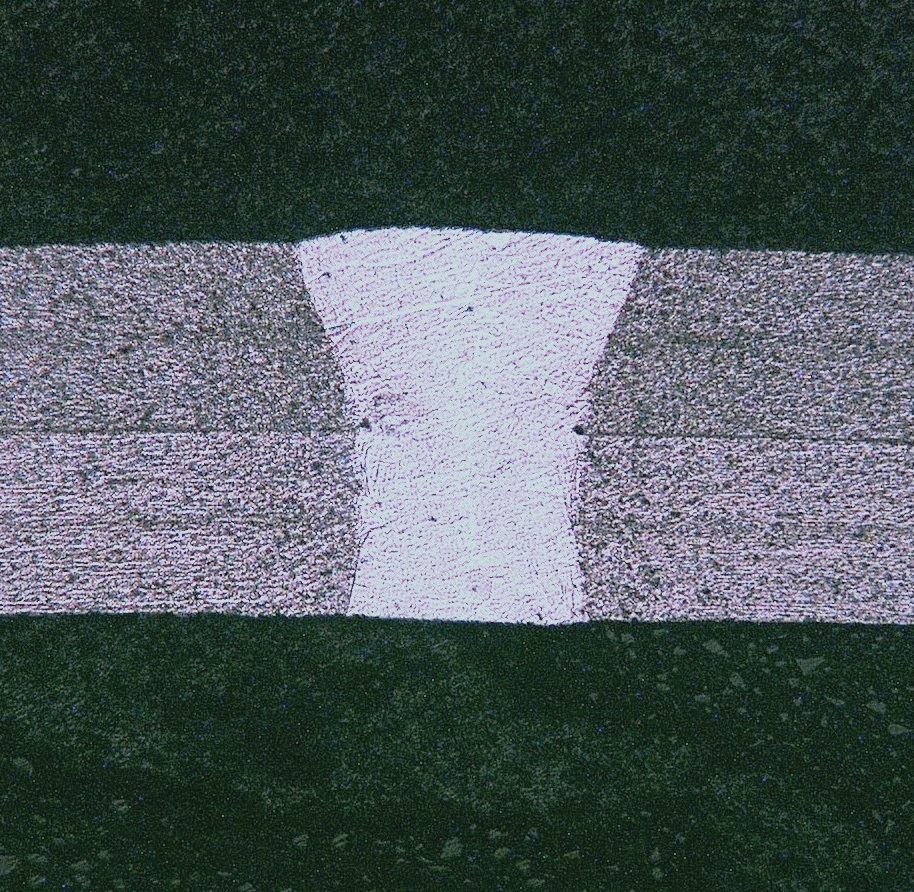
写真8 薄板の重ね溶接
写真9は異種金属の溶接である。アーク溶接が困難である黄銅(0.7mm)をステンレス鋼(1mm)に2m/minで重ね隅肉溶接をした。
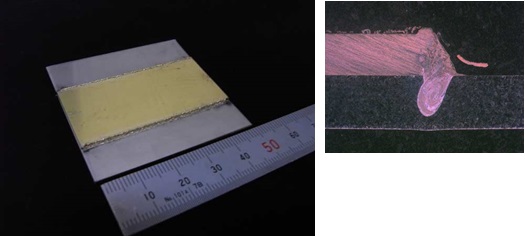
写真9 異種金属の溶接
写真10は金属と樹脂の接合である。ステンレス鋼(2mm)とナイロン(3mm)を1m/minで接合した。ステンレス鋼側からレーザを照射して加熱し、その熱によって溶融した界面のナイロンが溶着した。自動車などの輸送機器では車両軽量化による燃費向上が進んでおり、今後、金属と複合材料(CFRPなど)との直接接合が期待される。
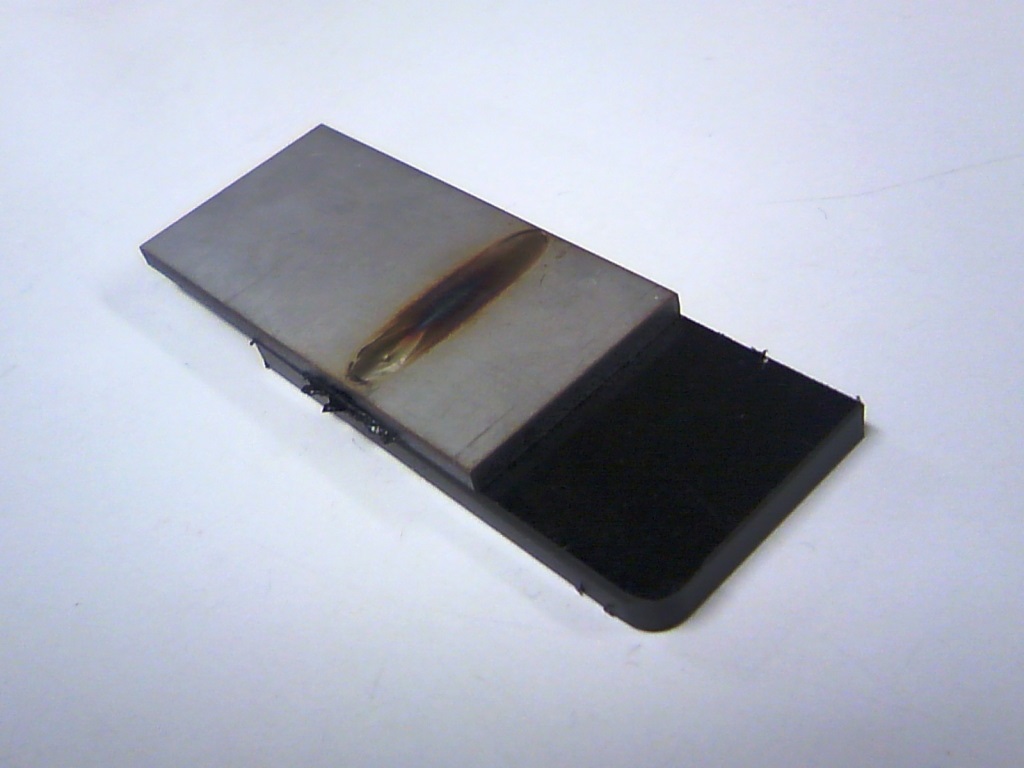
写真10 金属と樹脂の直接接合
(2)切断
写真11はパイプの切断である。アルミニウムパイプ(肉厚1mm)に2m/minで、自由な形状の切断(穴明け)をした。鉄鋼、アルミニウム、ニッケル・チタンの各合金・銅・銀などの切断ができる。また、ファイバーレーザなら、切断から溶接までを1台で加工することができる。
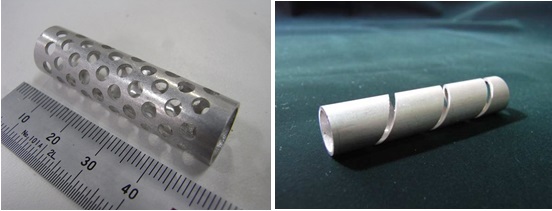
写真11 パイプの切断
(3)孔(穴)明け
写真12は孔(穴)明け加工の例である。ステンレス鋼(3mm)に、径3mm、112個の孔(穴)を明けた。加工時間は3分程度である。
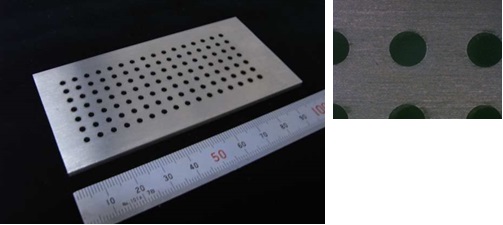
写真12 孔(穴)明け加工
4.2 シングルモードファイバーレーザの加工例
300W級のシングルモードファイバーレーザによる加工例を紹介する。
(1)溶接
写真13は薄板の重ね溶接である。燃料電池のセパレータの封止溶接を模擬したステンレス鋼(0.2mm)を30m/minの高速で溶接した。シングルモードではキーホールの径が細いので超高速溶接でもハンピングが発生しない。
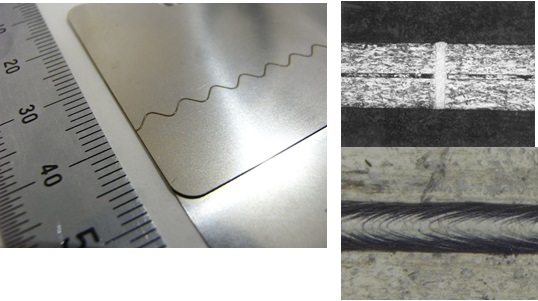
写真13 薄板の重ね溶接
写真14は薄板のヘリ継手の溶接である。ステンレス鋼(0.3mm)を8m/minで溶接した。写真15は薄板の角継手の溶接である。ステンレス鋼(0.5mm)を4m/minで溶接した。シングルモードの小さなビームスポットで高速溶接することにより、角部が溶融しない溶接ができる。
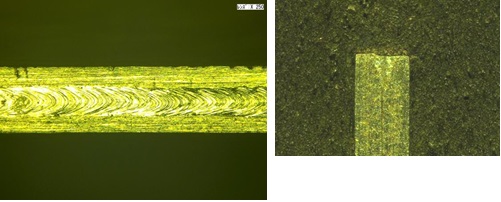
写真14 薄板のヘリ継手の溶接
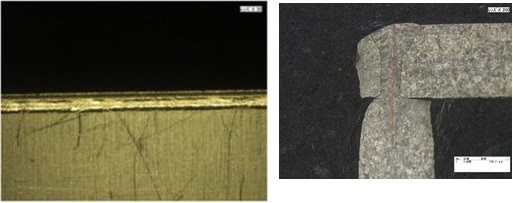
写真15 薄板の角継手の溶接
写真16は異種金属の重ね溶接である。アルミニウム(0.3mm)と銅(0.5mm)を2m/minで溶接した。高反射材の組み合わせであるが、シングルモードでビームスポットを約10μmに集光し、アルミニウム側からレーザを照射して接合した。
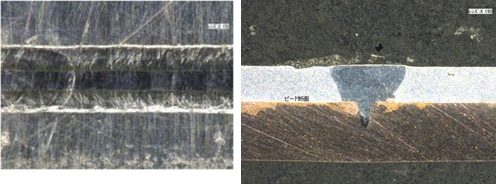
写真16 異種金属の重ね溶接
(2)切断
写真17はパイプの微細切断である。ステンレス鋼パイプ(外径6mm)を、高精度で鋭利な形状に切断した。
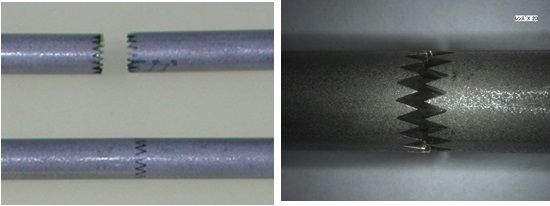
写真17 パイプの切断
写真18は細径チューブの切断である。ステンレス鋼チューブ(外径1.8mm)を部分的に微細切断して、フレキシブルチューブを製作した。
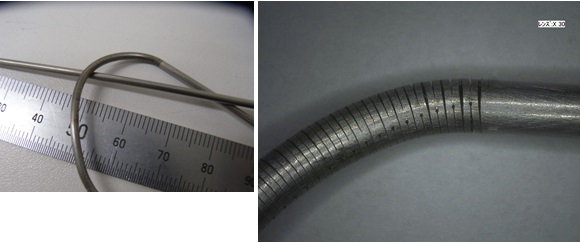
写真18 細径チューブの切断
写真19は薄鋼板の切断である。モータの電磁鋼板を模擬した鋼板(0.15mm)を30m/minで切断した。精細な切断形状の品質を確保するために、加工ステージの移動速度に同期したパルス制御によりレーザを照射した。
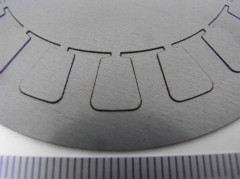
写真19 薄鋼板の切断
(3)孔(穴)明け
写真20は孔(穴)明け加工の例である。ステンレス鋼(1mm)に明けた径290,540,1015μmの孔(穴)形状である。
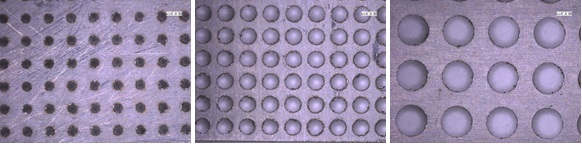
写真20 孔(穴)明け加工
(4)表面加工
「Laser Surfi-Sculpt®」加工法を紹介する。TWI(The Welding Institute)で開発され、電子ビームからレーザに発展した突起形成法である。図4に装置構成を示す。シングルモードファイバーレーザとビームスキャナーで構成される。樹脂と金属の接着強度、熱流体特性の向上などを目的に適用される7)。金属、セラミックスなどに高さ1mmを超える突起が形成できる。
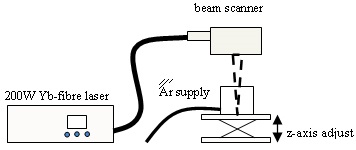
図4 装置構成
写真21は「Laser Surfi-Sculpt®」の加工例である。アルミニウム丸棒に高さ約2mmの突起が形成された。
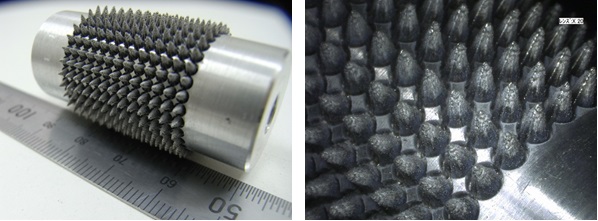
写真21 「Laser Surfi-Sculpt®」加工法
4.3 QCWファイバーレーザの加工例
平均出力150W級のQCWファイバーレーザによる加工例を紹介する。QCWレーザは高ピーク出力(例えば平均出力の10倍)のパルス発振が可能である。同時にCW発振の設定もあるので、幅広い加工に対応できる。小型、空冷、メンテナンスフリーで、今後、従来のパルスNd:YAGに替わる発振器として期待される。
(1)溶接
写真22は薄板の隅肉溶接である。チタン(0.5mm)を2m/minで溶接した。低入熱で酸化もなく、歪のない溶接ができた。
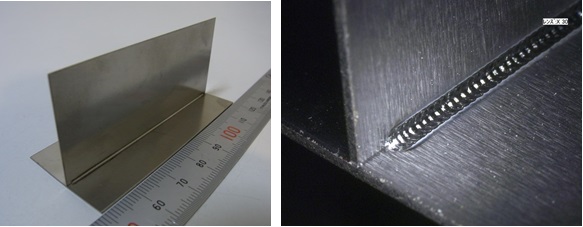
写真22 薄板の隅肉溶接 8)
(2)切断
写真4もQCWレーザの加工例である。写真23は中厚板の切断である。ステンレス鋼(5mm)を切断して、大出力レーザに比べて、高精度で鋭利な形状が得られた。
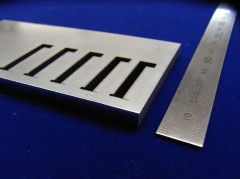
写真23 中厚板の切断
写真24は精細切断の加工例である。細いビームスポットとパルス発振による低入熱化で、0.1mmの微細なリブを製作した。
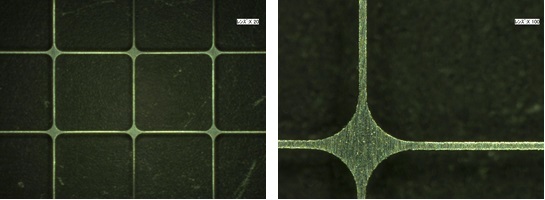
写真24 精細切断の加工例
4.4 パルスファイバーレーザの加工例
平均出力30W級のパルスファイバーレーザによる加工例を紹介する。パルスファイバーレーザは小型軽量で、パルス幅が短くピーク出力が高いので、高速穴明け、除去加工に使われる。
(1)溶接
写真25は極薄板の重ね溶接である。スキャナを用いて、チタン箔(3μm)を90m/minの高速で接合した。
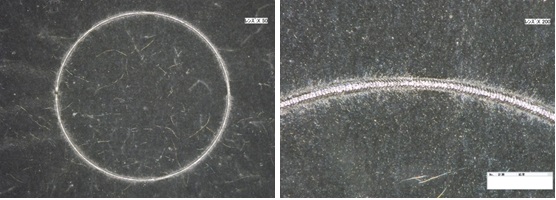
写真25 極薄板の重ね溶接
(2)孔(穴)明け
写真26は微細孔(穴)明け加工の例である。ニッケル箔(10μm)に径30μmの孔(穴)を明けた。写真27はアルミニウム箔(76μm)の場合で、入射側(左)径30μm、出射側(右)径20μmの孔(穴)が得られた。スキャナを用いてレーザ光を高速で走査することにより、良好な孔(穴)径の再現性と真円度で、300孔/杪の高速孔(穴)明け加工ができた。写真28は微細孔(穴)明け加工の応用を模擬して、アルミニウムにマーキングした例である。バックライトの透過光が確認できる。
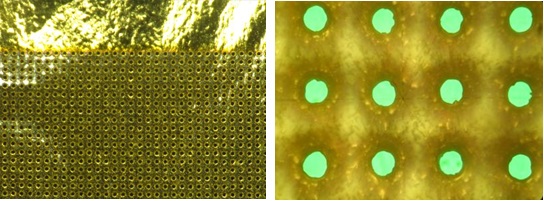
写真26 微細孔(穴)明け加工
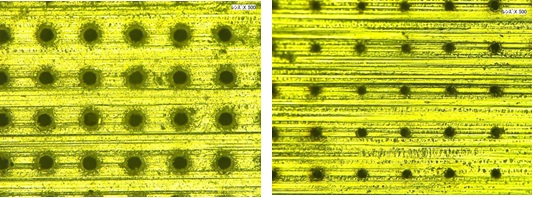
写真27 微細孔(穴)明け加工

写真28 微細孔(穴)明けの応用例
(3)表面加工
写真6もパルスファイバーレーザの加工例である。写真29は精密除去加工の例である。超硬材に溝を形成した。スキャナを用いてレーザ光を30m/minの高速で走査することにより、微小な深さ制御ができ、高精度で鋭利な加工ができた。写真30は精密除去加工の応用を模擬して、ステンレス鋼に、周囲を除去した漢字を描画した。
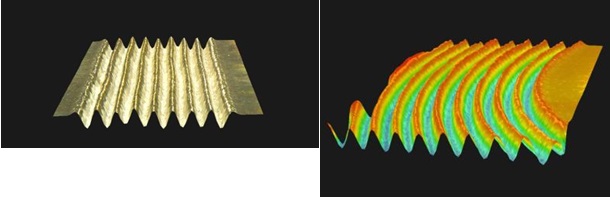
写真29 精密除去加工
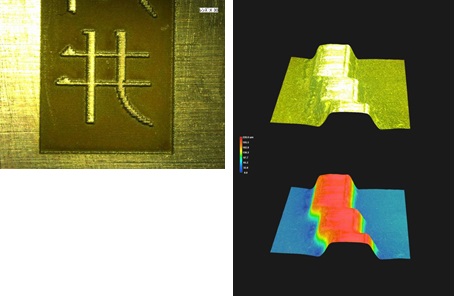
写真30 精密除去の応用例
「Clean-Lasersysteme」によるレーザクリーニングを紹介する。図5にレーザクリーニングの原理を示す。集光されたパルスレーザを除去層に吸収させ、アブレーションと呼ばれる昇華と、素材に与える微小な熱エネルギーの衝撃による表面破壊により除去加工が行われる。適用先は溶接の前洗浄、錆・酸化膜除去、接着の前処理、塗装剥離、金型の汚染物除去などである。その優位性は、乾式で薬品の副廃棄物がないこと、素材への影響の軽減、インラインでの処理などである9)。
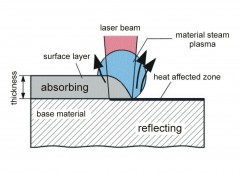
図5 レーザクリーニングの原理
写真31はレーザクリーニングの加工例である。左は鋼板上の赤錆を、右は黒色アルマイト皮膜を除去した。
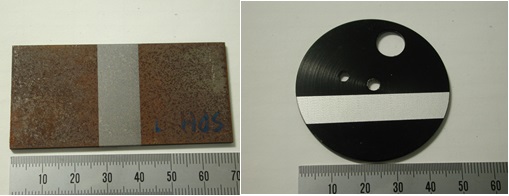
写真31 レーザクリーニング
5 おわりに
この度は精密加工の観点から、ファイバーレーザによる種々の加工例を紹介した。業界や製品別に分類することもできたが、掲載の可否などがあるので、実際に施工(試験)した加工例を発振器別に示した。その発振器も、海外だけではなく国内でも急速に開発、高性能化が進んでいる。ファイバーレーザに関して、すでに色々な誌面・講演などで報告されているが、実製品への適用についての紹介は少ないと思われるので、少しでも参考になれば幸いである。
参考文献
1) 荒谷:溶接技術, Vol.53, No.7, pp.155-160 (2005)など
2) 辻:高温学会誌, Vol.35, No.4, pp.171-175 (2009)
3) IPGフォトニクスジャパン(株):WEB資料
4) IPGフォトニクスジャパン(株):カタログ
5) 特集:OPTRONICS, No.4 (2006)
6) 特集:レーザ協会誌, Vol.28, No.2 (2003)
7) TWI:WEB資料
8) 第6回レーザー加工技術展で入手 (2013-4)
9) 本村:溶接技術, Vol.56, No.11, pp.69-71 (2008)
レーザ加工の事ならおまかせ!
本サイト運営会社レーザックスの紹介はこちら!
運営会社紹介ページへ
レーザに関する情報が盛りだくさん!
レーザ加工なびTOPへ