シングルモードファイバーレーザの可能性
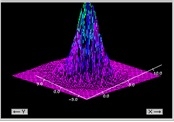
「溶接技術」平成20年11月号より
シングルモードファイバーレーザの可能性
株式会社レーザックス 荒谷 雄
1.はじめに
ファイバー伝送できる従来の固体レーザはビーム伝送中に光の位相ずれなどで、出力ビームは一般的にマルチモードになり、エネルギー分布はトップハット型(山高帽型)を示すため、溶接に多用されている。一方近年開発されたシングルモードの固体レーザは必然的に極細径ファイバーでビーム伝送することでエネルギー分布がガウス分布のままで伝送され、切断加工や穴加工にも有効なビームとなる。
一方ガスレーザのCO2レーザはガウス分布のビームモードをファイバー伝送することができず、ミラー伝送するためガウス分布ビームとなり、切断加工に多用されている。
固体レーザとCO2レーザの基本特性の相違はこのビームモードの他に、レーザのビーム品質評価に使用されるBPP(ビームパラメータプロダクツ)が異なる。BPPは焦点位置でのビーム径と広がり角の積であるが、ビームの焦点径は光波長に比例するので、理論上Nd:YAGレーザの焦点はCO2レーザの1/10に集光でき、BPPも1/10になる。しかしマルチモードの高出力ビームをファイバー伝送するとBPPがCO2レーザより低下してしまう。またCO2レーザは10.6μmの長波長のため材料表面での反射が大きく、またキーホールで発生したプラズマにレーザビームが吸収されるため、溶接や厚板切断ではHeガスでのプラズマ除去が必要であった。
これまではCO2レーザの高出力化が進み、最大40kWクラスまで市場に出ていた。しかし近年、高出力のNd:YAGレーザや半導体レーザ等の固体レーザの開発が進み市場に出てくると、先に述べたビーム特性や基本特性の相違により、接合加工に向く発振器として製造業界に浸透してきた。
一方シングルモードのファイバーレーザ、即ちエネルギー強度がガウス分布のファイバーレーザの高出力化も平行して欧米で開発が進み、100Wクラスが2000年に市販されて以来、図1に示すように急速な出力向上が図られ、今では2kWまで市販され、2007年には3kWも開発されている1)。また国内でもすでに2kWのシングルモードファイバーレーザが導入されている。その結果、産業界では先に述べたトップハット型の固体レーザが持つ特徴の他に、エネルギー分布がCO2レーザと同じガウス分布で、理論ビーム径がCO2レーザの1/10の超高密度熱源として、高精度な溶接のみならず、精密切断やマイクロ孔(穴)・溝加工の面でも注目を浴びることになった。
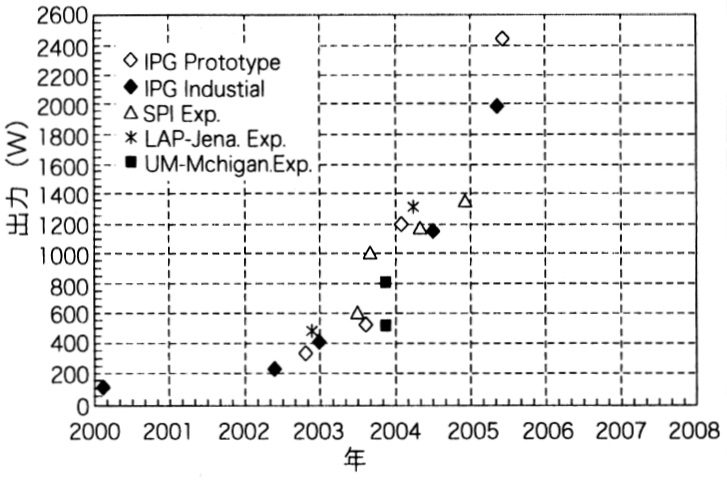
図1 シングルモードYbファイバーレーザの出力推移
シングルモードファイバーレーザはまだ実用例が少なく、その可能性は計り知れないものがあるが、本稿ではこの発振器および加工例の知るところを述べる事で、皆様のご参考になればと存じます。
2.ファイバーレーザの発振原理と主な特徴
固体レーザにはNd:YAGレーザ、ディスクレーザ、半導体レーザおよびファイバー自身が発振器となるファイバーレーザがある。この中で、ファイバーレーザ発振器の原理と基本構成を図2に示したが、図中に示すようにダブルクラッドファイバーの内側クラッドに外付けファイバーを介して励起光を導入し、これを外側クラッドとの界面で全反射させながら伝播させることで、Ybをドーピングしたコアファイバーを効率よく励起している。さらにこのコアファイバーの両端には回折格子が埋め込まれており、光をFBG理論で反射させて増幅している。従って、このレーザは反射ミラーを使用せずに効率よく共振・増幅できる特徴を持っている。なお励起光は光通信仕様のLD(保証時間:100,000Hr)を使用している。コアファイバーの径は9μm程度でシングルモードの光が得られる。先の図2に示したファイバーレーザの1モジュールは約400W-600Wのシングルモードビームの出力が得られている。同図中にこの励起用LDとモジュールの外観写真を示した。
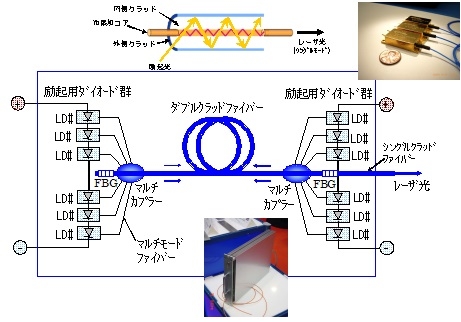
図2 ファイバーレーザモジュールの原理と基本構成
このモジュールを並列に接続すると出力がその数に比例して増幅されマルチモード化する。国内では20kWまで市販されているが、今年IPG社では30kW、ファイバー径0.2μmの高出力な発振器を発表している3)。
また発振効率はランプ励起Nd:YAGレーザが数%、LD励起Nd:YAGレーザ、ディスクレーザおよびCO2レーザがそれぞれ約15%で、これらと比較してファイバーレーザおよび半導体レーザは発振効率が25-30%と高いので、冷却設備の負担が少なく、設備として空冷チラーがあれば良く、クーリングタワーは不要となる。
またファイバーレーザはビーム品質が良いため20kWでも径0.2mmの細径のファーバーで光伝送ができ、集光径が小さいため高エネルギー密度の加工ができる。
従って加工の面では、ファイバーレーザは先に述べたような特性から、溶接と切断の共用化が進められている。さらにBPPが良いため遠距離(リモート)加工ができるので、近年はリモート溶接の適用検討も進められている。
なおファイバーレーザはドーピング材のYbに代わりErやTmを使用することで発振波長を変えることができる。またパルスレーザ、フェムト秒レーザ、グリーンレーザ、UVレーザ、等の各種シングルモード/マルチモードのファイバーレーザ発振器も開発されているが、本稿では略す。
3.シングルモード発振器の特性
ファイバーレーザのシングルモードビームは先の図2に示したモジュール単体から得られるが、高出力のシングルモードビームは図3に示すように、このモジュールを直列接続して出力を増幅している2),3)。
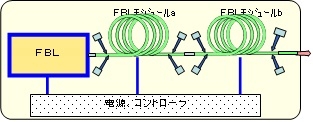
図3 シングルモードファイバーレーザの基本構成 [直列増幅]
2005年の6月に写真1に示すような2kWのシングルモードファイバーレーザ発振器が発表された。このファイバー径は14μmである。このプロファイルデータは図4に示すように、モード:TEM00、M2:1.2が得られており、BPPに換算すると0.4mm*mradとなり、13,000kW/mm2と言う超高密度なエネルギーが得られている。
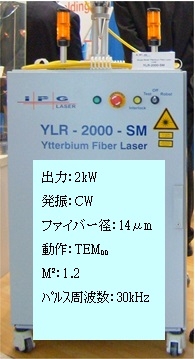
写真1 2kWシングルモードファイバーレーザの外観
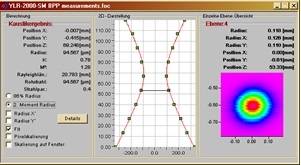
図4 2kWシングルモードのプロファイル
300W以下の発振器は空冷で、ファイバー径が9μm、プロファイルは図5に示すようにTEM00のビームが得られ、M2は1.05でBPPに換算すると0.35mm*mradとなる。エネルギー密度は4,718kW/mm2の非常に高い値となる。
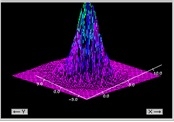
図5 プロファイル(300W)
従来のファイバーレーザやディスクレーザのエネルギー密度は150-250kW/mm2、Nd:YAGレーザが14-16kW/mm2から考えると、いかにエネルギー密度が高いかが分かる。
また発振器は基本的にCW発振であるが、最大変調周波数が30kHzと高く、効果的なパルス加工が可能で、従来のQ-スイッチNd:YAGレーザの加工領域もカバーすることができるかと考える。
図6に示すオシロ波形の上のラインは外部から入力したTTL信号の20kHzを示し、発振した出力を下のラインに示す。その結果、発振応答の遅れ時間が5μS程度で、25μSのパルス出力が確保されている事が分かる3)。
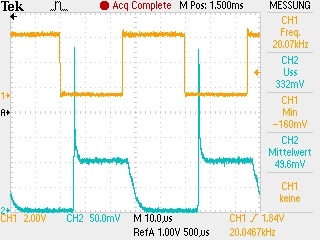
図6 矩形波変調波形(20kHz) 上:入力、下:出力
また出力はゼロから最大までON/OFF制御ができるので、Nd:YAGレーザでは必要な数十Wのシーマ出力が不要となり、その結果メカニカルシャッターが無くなった。
また図7の上のラインは外部から入力した80Hzの三角波信号を示し、さらに発振器内部制御で、1kHz、Duty30%の変調を掛けて出力した波形を下のラインに示している。その結果同図に示すように300μSの出力が80Hzの中で12パルス出ている3)。
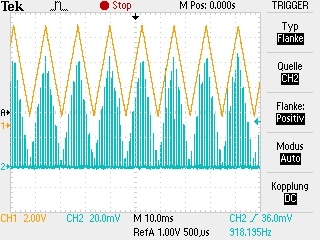
図7 三角波30%Duty波形 上:入力、下:出力 (TTL: 80Hz、内部制御:1kHz)
このようにシングルモードファイバーレーザはビーム出力を高い周波数応答で制御できるので、加工用途に応じて幅広い条件設定ができる特徴を持っている。
4.加工特性および加工例
4.1 溶接加工
一般に溶接速度が速くなるとビードにハンピングが生じるが、シングルモードではビーム径が細く、且つエネルギー密度が高いので溶融金属の流れが減速され6m/min以上の高速度溶接でもハンピングが発生しない1)。
弊社の300Wシングルモードファイバーレーザを使用して突合せ溶接した一例を写真2に示すが、出力:75W、速度:10m/minの高速度でSUS304(0.1t)を溶接した結果、アンダーカットや過剰余盛のない良好な溶接継手が得られている。シールドガスはN2を使用している。
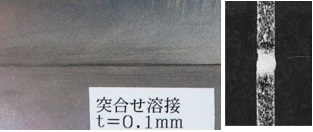
写真2 薄板(SUS304)の溶接例、発振器:IPG300WSM
BIASでは写真3に示すように200Wシングルモードファイバーレーザを使用してステンレス鋼板(SUS316)にBOP溶接を行ったが、120m/minの速度でもハンピングのない溶接ができている6)。この発振器のBPPは<0.5mm*mrad、ファイバー径は7μm、焦点径は10μmである。
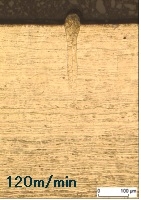
写真3 SUS316のBOP溶接
従って、このような高速度溶接は従来の加工機で実現するのは難しく、ガルバーミラー型の光学ヘッドを利用したシステムの開発が進展するかと考える。
また写真4は異材の重ね継手を高速度で溶接した例を示す6)。シングルモードファイバーレーザを使用し、出力:200W、焦点径:10μm、溶接速度:20m/minで溶接している。上板は板厚100μmの純銅(E-Cu58)で下板は板厚100μmのSUS316である。その結果、エネルギー密度が高く、またキーホールが細く、かつ高速度で移動するので、上下の溶融金属は混ざり合わずに接合している。
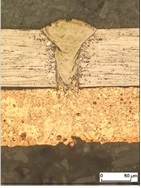
写真4 異材の重ね溶接(40m/min、200W、100μm)上板:SUS316、下板:純Cu
従って脆い金属間化合物が形成しやすい異材金属の接合に利用できる接合法の一つかと考える。
また2次元のガルバー式スキャナーを利用して高速度のマイクロ溶接を行った例を写真5に示す。板厚0.3mmの銅板(E-Cu58)を2枚重ねて焦点径25μm、200Wのシングルモードレーザで円弧溶接している。詳細条件は不明であるが、直径約100μmの貫通溶接ができている。
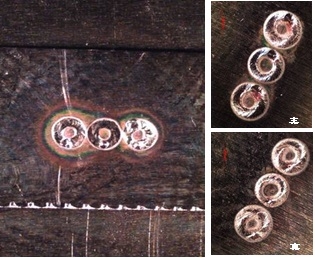
写真5 重ね継手銅板(0.3mmx2)の円弧スキャナー溶接
また写真6はステンレス鋼のフランジの角継手に楔状にレーザ溶接を行ったときの断面マクロである3)。この溶接は400Wシングルモードファイバーレーザを用い、出力:180W、溶接速度:2m/minで1mm以上の溶込み深さが得られている。
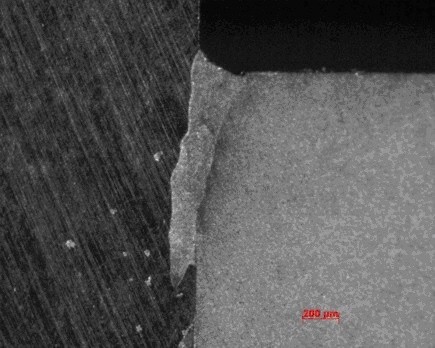
写真6 ステンレス鋼フランジの角継手レーザ溶接
4.2 孔(穴)加工
孔(穴)加工の方法にはレーザのシングル/マルチパルスによる孔(穴)加工と、トレパニングによる孔(穴)加工があり、両者の例を写真7、写真8に示した3)。写真7はSUS304(板厚25.4μm)に径40μmの孔(穴)加工を行った例で、平均レーザ出力:5W、パルス時間:50μSの条件で1,000孔/秒の孔(穴)加工を行っている。また写真8はSUS304(板厚127μm)にトレパニングで径100μmの孔(穴)加工を行った例で、平均レーザ出力:10W、パルス幅:60μS、パルス周波数:1.5kHz、切断速度:760mm/minで加工している。なお両者ともアシストガスに酸素を使用している。
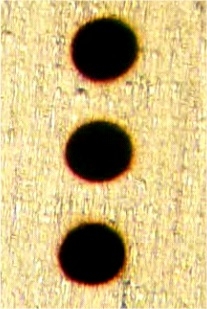
写真7 シングルパルス孔(穴)加工
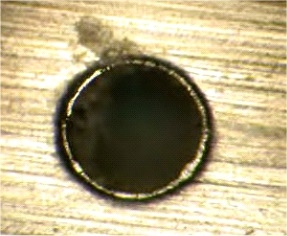
写真8 トレパニング孔(穴)加工
前者の場合は高速度に孔(穴)加工ができるが、孔(穴)形状がビーム形状に依存するため、少しいびつになっている。後者のトレパニング加工では孔(穴)形状に沿ってビームを走らせるため、加工後の形状は機械精度に依存するが、同写真に示すように良好な円弧が得られる。しかし切断速度は幾分低下し、孔径もビーム径より少し大きくなる。
多数の孔(穴)加工を行うためにスキャナー加工が開発されており、写真9の例は2次元のガルバー式ミラー(Scanlab Hurryscan II)を使用して100Wのシングルモードファイバーレーザでステンレス鋼(板厚0.1mm)に160孔/秒をあけている。焦点長さ100mmの集光レンズを使用し、集光径30μm、ピッチ200mmの孔(穴)を出力1mJ@20kHzのビームを125パルス/孔(0.125J/孔)照射して加工している3)。
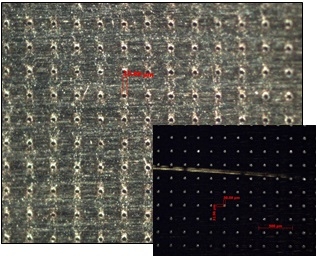
写真9 ステンレス鋼板のスキャナー孔(穴)加工
4.3 切断加工
切断加工は一般的にCO2レーザで行われているが、鋼材(St 1203、板厚:1mm)を1kWのシングルモードファイバーレーザと2.5kWのCO2レーザで出力ごとに切断速度を比較した例を図8に示す4)。この結果によると、切断速度はシングルモードファイバーレーザが約2倍の高速度で切断できることを示している。この比較データではアシストガスに1MPaのN2を使用しており、ノズル径:1.5mm、スタンドオフ:1mm、焦点長さ:120mm、焦点位置:-1mmと同じ値に設定しているが、集光径がファイバーレーザでは15μm、CO2では140μmと異なり、この差が切断速度の差になっているものと考える。また表面の切断幅は前者が100μm、後者が120μmである4)。
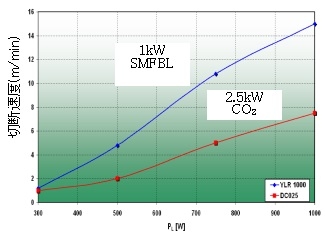
図8 シングルモードファイバーレーザとCO2レーザの切断速度
また表面粗さは写真10に示すように、板厚5mmの同鋼材(St1203)を切断した場合は非常に滑らかで、表面粗さRa(中心線平均粗さ)は2μm、Rz(10点の平均粗さ)は9μmである4)。この切断には出力1kWのシングルモードファイバーレーザを用い、4m/minの速度で切断している。アシストガスは酸素である。
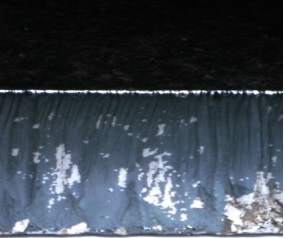
写真10 1kWシングルモードレーザ切断の表面粗さ(Ra: ca. 2μm、Rz: ca. 9μm)
また板厚3mmのステンレス鋼 (18Cr10Ni)のデータでは表面粗さはRa:7μm、Rz:41μmを示している5)。CO2レーザと比較した結果ではシングルモードは約2倍の高速度で切断できるが、表面粗さは2倍ほど粗くなっている様に感じる。
非金属材料の切断加工はセラミックスが多いが、弊社でサファイヤガラスを切断した例を写真11に示す。板厚1.5mmのサファイヤ板ガラスをシングルモードファイバーを用い、出力300W、速度300mm/minで切断した例であるが、良好な切断面が得られた。アシストガスは0.6MPaのN2ガスで、レーザ波形は500Hz、Duty30%である。
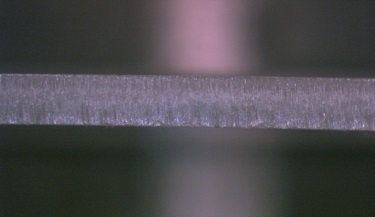
写真11 サファイヤガラスの切断
また同材の孔(穴)加工も行っているが、その際は1kHzでDuty10%のパルス波形を使用している。
従来、この材料は他の発振器での加工は困難であったが、高いエネルギー密度を照射できた結果、このような加工ができたものと考える。
5.おわりに
シングルモードファイバーレーザは近年3kW級まで高出力化が進み、にわかに注目を浴びているが、これにより理論限界に近いビーム品質が高出力で得られ、超高エネルギー密度の加工ができるようになった。言い換えれば、現実に直径15μmの所に数kWのレーザビームを照射することができるようになった。その結果、溶接、切断および孔(穴)・溝加工ではより超高速度な加工、高精密な加工が実現できるようになった。また異材溶接では従来と異なる溶融・凝固現象を示しているが、まだ未知の部分が多い。
本稿がものづくりエンジニヤの方々の参考になればこの上なく幸甚に存じます。
参考文献
1) 宮本、高出力ファイバーレーザによる加工、 O plus E、Vol.27, No.11, 2005-11
2) 荒谷、高出力ファイバーレーザとその加工特性、溶接技術、2006-8
3) IPG技術資料、2007
4) Morgenthal,L, Cutting with Fiber Lasers, 1st IFW, 2005-11
5) Himmer, T., High Brightness Laser in Cutting Applicasions, ICALEO, 2007-10
6) Seefeld,T, Welding with Fiber laser BLZ-Semminar, 2005-4
レーザ加工の事ならおまかせ!
本サイト運営会社レーザックスの紹介はこちら!
運営会社紹介ページへ
レーザに関する情報が盛りだくさん!
レーザ加工なびTOPへ
シングルモードファイバーレーザの可能性
株式会社レーザックス 荒谷 雄
1.はじめに
ファイバー伝送できる従来の固体レーザはビーム伝送中に光の位相ずれなどで、出力ビームは一般的にマルチモードになり、エネルギー分布はトップハット型(山高帽型)を示すため、溶接に多用されている。一方近年開発されたシングルモードの固体レーザは必然的に極細径ファイバーでビーム伝送することでエネルギー分布がガウス分布のままで伝送され、切断加工や穴加工にも有効なビームとなる。
一方ガスレーザのCO2レーザはガウス分布のビームモードをファイバー伝送することができず、ミラー伝送するためガウス分布ビームとなり、切断加工に多用されている。
固体レーザとCO2レーザの基本特性の相違はこのビームモードの他に、レーザのビーム品質評価に使用されるBPP(ビームパラメータプロダクツ)が異なる。BPPは焦点位置でのビーム径と広がり角の積であるが、ビームの焦点径は光波長に比例するので、理論上Nd:YAGレーザの焦点はCO2レーザの1/10に集光でき、BPPも1/10になる。しかしマルチモードの高出力ビームをファイバー伝送するとBPPがCO2レーザより低下してしまう。またCO2レーザは10.6μmの長波長のため材料表面での反射が大きく、またキーホールで発生したプラズマにレーザビームが吸収されるため、溶接や厚板切断ではHeガスでのプラズマ除去が必要であった。
これまではCO2レーザの高出力化が進み、最大40kWクラスまで市場に出ていた。しかし近年、高出力のNd:YAGレーザや半導体レーザ等の固体レーザの開発が進み市場に出てくると、先に述べたビーム特性や基本特性の相違により、接合加工に向く発振器として製造業界に浸透してきた。
一方シングルモードのファイバーレーザ、即ちエネルギー強度がガウス分布のファイバーレーザの高出力化も平行して欧米で開発が進み、100Wクラスが2000年に市販されて以来、図1に示すように急速な出力向上が図られ、今では2kWまで市販され、2007年には3kWも開発されている1)。また国内でもすでに2kWのシングルモードファイバーレーザが導入されている。その結果、産業界では先に述べたトップハット型の固体レーザが持つ特徴の他に、エネルギー分布がCO2レーザと同じガウス分布で、理論ビーム径がCO2レーザの1/10の超高密度熱源として、高精度な溶接のみならず、精密切断やマイクロ孔(穴)・溝加工の面でも注目を浴びることになった。
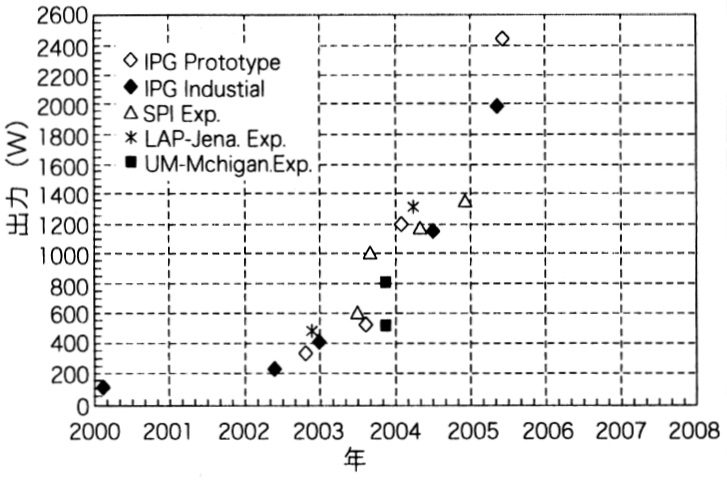
図1 シングルモードYbファイバーレーザの出力推移
シングルモードファイバーレーザはまだ実用例が少なく、その可能性は計り知れないものがあるが、本稿ではこの発振器および加工例の知るところを述べる事で、皆様のご参考になればと存じます。
2.ファイバーレーザの発振原理と主な特徴
固体レーザにはNd:YAGレーザ、ディスクレーザ、半導体レーザおよびファイバー自身が発振器となるファイバーレーザがある。この中で、ファイバーレーザ発振器の原理と基本構成を図2に示したが、図中に示すようにダブルクラッドファイバーの内側クラッドに外付けファイバーを介して励起光を導入し、これを外側クラッドとの界面で全反射させながら伝播させることで、Ybをドーピングしたコアファイバーを効率よく励起している。さらにこのコアファイバーの両端には回折格子が埋め込まれており、光をFBG理論で反射させて増幅している。従って、このレーザは反射ミラーを使用せずに効率よく共振・増幅できる特徴を持っている。なお励起光は光通信仕様のLD(保証時間:100,000Hr)を使用している。コアファイバーの径は9μm程度でシングルモードの光が得られる。先の図2に示したファイバーレーザの1モジュールは約400W-600Wのシングルモードビームの出力が得られている。同図中にこの励起用LDとモジュールの外観写真を示した。
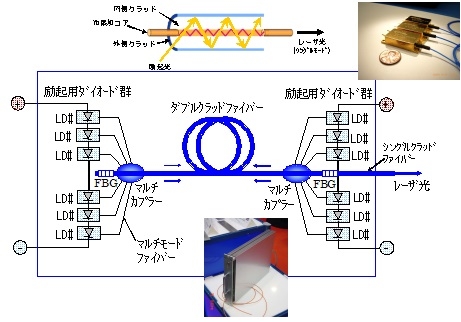
図2 ファイバーレーザモジュールの原理と基本構成
このモジュールを並列に接続すると出力がその数に比例して増幅されマルチモード化する。国内では20kWまで市販されているが、今年IPG社では30kW、ファイバー径0.2μmの高出力な発振器を発表している3)。
また発振効率はランプ励起Nd:YAGレーザが数%、LD励起Nd:YAGレーザ、ディスクレーザおよびCO2レーザがそれぞれ約15%で、これらと比較してファイバーレーザおよび半導体レーザは発振効率が25-30%と高いので、冷却設備の負担が少なく、設備として空冷チラーがあれば良く、クーリングタワーは不要となる。
またファイバーレーザはビーム品質が良いため20kWでも径0.2mmの細径のファーバーで光伝送ができ、集光径が小さいため高エネルギー密度の加工ができる。
従って加工の面では、ファイバーレーザは先に述べたような特性から、溶接と切断の共用化が進められている。さらにBPPが良いため遠距離(リモート)加工ができるので、近年はリモート溶接の適用検討も進められている。
なおファイバーレーザはドーピング材のYbに代わりErやTmを使用することで発振波長を変えることができる。またパルスレーザ、フェムト秒レーザ、グリーンレーザ、UVレーザ、等の各種シングルモード/マルチモードのファイバーレーザ発振器も開発されているが、本稿では略す。
3.シングルモード発振器の特性
ファイバーレーザのシングルモードビームは先の図2に示したモジュール単体から得られるが、高出力のシングルモードビームは図3に示すように、このモジュールを直列接続して出力を増幅している2),3)。
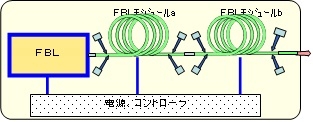
図3 シングルモードファイバーレーザの基本構成 [直列増幅]
2005年の6月に写真1に示すような2kWのシングルモードファイバーレーザ発振器が発表された。このファイバー径は14μmである。このプロファイルデータは図4に示すように、モード:TEM00、M2:1.2が得られており、BPPに換算すると0.4mm*mradとなり、13,000kW/mm2と言う超高密度なエネルギーが得られている。
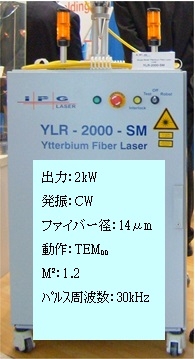
写真1 2kWシングルモードファイバーレーザの外観
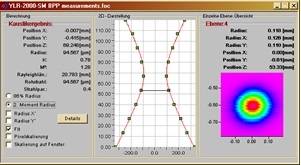
図4 2kWシングルモードのプロファイル
300W以下の発振器は空冷で、ファイバー径が9μm、プロファイルは図5に示すようにTEM00のビームが得られ、M2は1.05でBPPに換算すると0.35mm*mradとなる。エネルギー密度は4,718kW/mm2の非常に高い値となる。
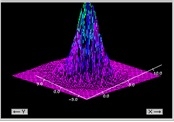
図5 プロファイル(300W)
従来のファイバーレーザやディスクレーザのエネルギー密度は150-250kW/mm2、Nd:YAGレーザが14-16kW/mm2から考えると、いかにエネルギー密度が高いかが分かる。
また発振器は基本的にCW発振であるが、最大変調周波数が30kHzと高く、効果的なパルス加工が可能で、従来のQ-スイッチNd:YAGレーザの加工領域もカバーすることができるかと考える。
図6に示すオシロ波形の上のラインは外部から入力したTTL信号の20kHzを示し、発振した出力を下のラインに示す。その結果、発振応答の遅れ時間が5μS程度で、25μSのパルス出力が確保されている事が分かる3)。
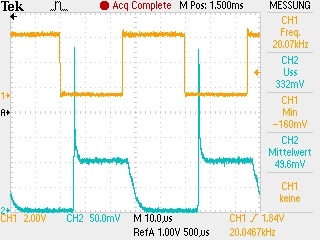
図6 矩形波変調波形(20kHz) 上:入力、下:出力
また出力はゼロから最大までON/OFF制御ができるので、Nd:YAGレーザでは必要な数十Wのシーマ出力が不要となり、その結果メカニカルシャッターが無くなった。
また図7の上のラインは外部から入力した80Hzの三角波信号を示し、さらに発振器内部制御で、1kHz、Duty30%の変調を掛けて出力した波形を下のラインに示している。その結果同図に示すように300μSの出力が80Hzの中で12パルス出ている3)。
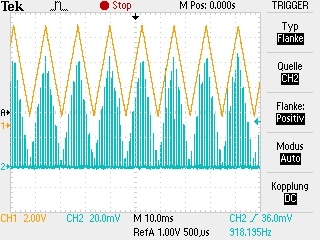
図7 三角波30%Duty波形 上:入力、下:出力 (TTL: 80Hz、内部制御:1kHz)
このようにシングルモードファイバーレーザはビーム出力を高い周波数応答で制御できるので、加工用途に応じて幅広い条件設定ができる特徴を持っている。
4.加工特性および加工例
4.1 溶接加工
一般に溶接速度が速くなるとビードにハンピングが生じるが、シングルモードではビーム径が細く、且つエネルギー密度が高いので溶融金属の流れが減速され6m/min以上の高速度溶接でもハンピングが発生しない1)。
弊社の300Wシングルモードファイバーレーザを使用して突合せ溶接した一例を写真2に示すが、出力:75W、速度:10m/minの高速度でSUS304(0.1t)を溶接した結果、アンダーカットや過剰余盛のない良好な溶接継手が得られている。シールドガスはN2を使用している。
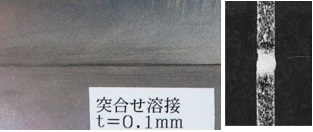
写真2 薄板(SUS304)の溶接例、発振器:IPG300WSM
BIASでは写真3に示すように200Wシングルモードファイバーレーザを使用してステンレス鋼板(SUS316)にBOP溶接を行ったが、120m/minの速度でもハンピングのない溶接ができている6)。この発振器のBPPは<0.5mm*mrad、ファイバー径は7μm、焦点径は10μmである。
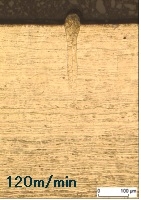
写真3 SUS316のBOP溶接
従って、このような高速度溶接は従来の加工機で実現するのは難しく、ガルバーミラー型の光学ヘッドを利用したシステムの開発が進展するかと考える。
また写真4は異材の重ね継手を高速度で溶接した例を示す6)。シングルモードファイバーレーザを使用し、出力:200W、焦点径:10μm、溶接速度:20m/minで溶接している。上板は板厚100μmの純銅(E-Cu58)で下板は板厚100μmのSUS316である。その結果、エネルギー密度が高く、またキーホールが細く、かつ高速度で移動するので、上下の溶融金属は混ざり合わずに接合している。
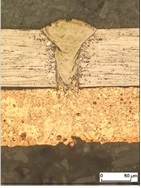
写真4 異材の重ね溶接(40m/min、200W、100μm)上板:SUS316、下板:純Cu
従って脆い金属間化合物が形成しやすい異材金属の接合に利用できる接合法の一つかと考える。
また2次元のガルバー式スキャナーを利用して高速度のマイクロ溶接を行った例を写真5に示す。板厚0.3mmの銅板(E-Cu58)を2枚重ねて焦点径25μm、200Wのシングルモードレーザで円弧溶接している。詳細条件は不明であるが、直径約100μmの貫通溶接ができている。
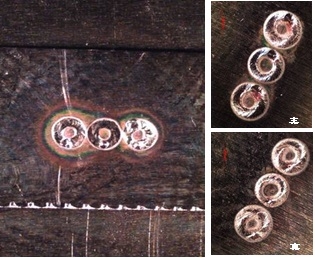
写真5 重ね継手銅板(0.3mmx2)の円弧スキャナー溶接
また写真6はステンレス鋼のフランジの角継手に楔状にレーザ溶接を行ったときの断面マクロである3)。この溶接は400Wシングルモードファイバーレーザを用い、出力:180W、溶接速度:2m/minで1mm以上の溶込み深さが得られている。
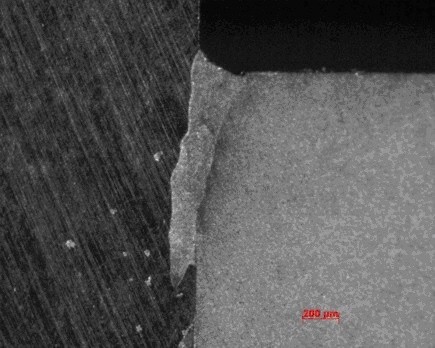
写真6 ステンレス鋼フランジの角継手レーザ溶接
4.2 孔(穴)加工
孔(穴)加工の方法にはレーザのシングル/マルチパルスによる孔(穴)加工と、トレパニングによる孔(穴)加工があり、両者の例を写真7、写真8に示した3)。写真7はSUS304(板厚25.4μm)に径40μmの孔(穴)加工を行った例で、平均レーザ出力:5W、パルス時間:50μSの条件で1,000孔/秒の孔(穴)加工を行っている。また写真8はSUS304(板厚127μm)にトレパニングで径100μmの孔(穴)加工を行った例で、平均レーザ出力:10W、パルス幅:60μS、パルス周波数:1.5kHz、切断速度:760mm/minで加工している。なお両者ともアシストガスに酸素を使用している。
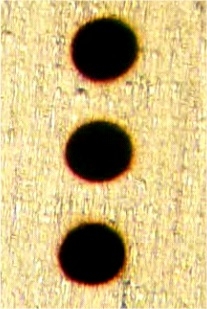
写真7 シングルパルス孔(穴)加工
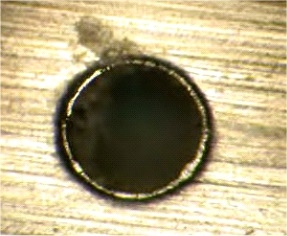
写真8 トレパニング孔(穴)加工
前者の場合は高速度に孔(穴)加工ができるが、孔(穴)形状がビーム形状に依存するため、少しいびつになっている。後者のトレパニング加工では孔(穴)形状に沿ってビームを走らせるため、加工後の形状は機械精度に依存するが、同写真に示すように良好な円弧が得られる。しかし切断速度は幾分低下し、孔径もビーム径より少し大きくなる。
多数の孔(穴)加工を行うためにスキャナー加工が開発されており、写真9の例は2次元のガルバー式ミラー(Scanlab Hurryscan II)を使用して100Wのシングルモードファイバーレーザでステンレス鋼(板厚0.1mm)に160孔/秒をあけている。焦点長さ100mmの集光レンズを使用し、集光径30μm、ピッチ200mmの孔(穴)を出力1mJ@20kHzのビームを125パルス/孔(0.125J/孔)照射して加工している3)。
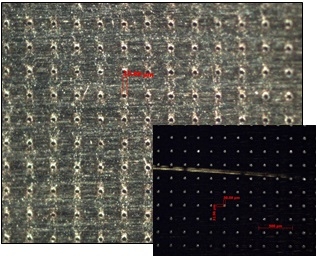
写真9 ステンレス鋼板のスキャナー孔(穴)加工
4.3 切断加工
切断加工は一般的にCO2レーザで行われているが、鋼材(St 1203、板厚:1mm)を1kWのシングルモードファイバーレーザと2.5kWのCO2レーザで出力ごとに切断速度を比較した例を図8に示す4)。この結果によると、切断速度はシングルモードファイバーレーザが約2倍の高速度で切断できることを示している。この比較データではアシストガスに1MPaのN2を使用しており、ノズル径:1.5mm、スタンドオフ:1mm、焦点長さ:120mm、焦点位置:-1mmと同じ値に設定しているが、集光径がファイバーレーザでは15μm、CO2では140μmと異なり、この差が切断速度の差になっているものと考える。また表面の切断幅は前者が100μm、後者が120μmである4)。
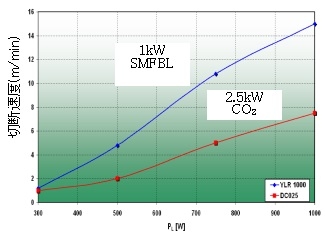
図8 シングルモードファイバーレーザとCO2レーザの切断速度
また表面粗さは写真10に示すように、板厚5mmの同鋼材(St1203)を切断した場合は非常に滑らかで、表面粗さRa(中心線平均粗さ)は2μm、Rz(10点の平均粗さ)は9μmである4)。この切断には出力1kWのシングルモードファイバーレーザを用い、4m/minの速度で切断している。アシストガスは酸素である。
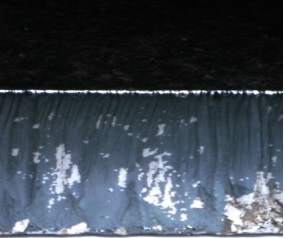
写真10 1kWシングルモードレーザ切断の表面粗さ(Ra: ca. 2μm、Rz: ca. 9μm)
また板厚3mmのステンレス鋼 (18Cr10Ni)のデータでは表面粗さはRa:7μm、Rz:41μmを示している5)。CO2レーザと比較した結果ではシングルモードは約2倍の高速度で切断できるが、表面粗さは2倍ほど粗くなっている様に感じる。
非金属材料の切断加工はセラミックスが多いが、弊社でサファイヤガラスを切断した例を写真11に示す。板厚1.5mmのサファイヤ板ガラスをシングルモードファイバーを用い、出力300W、速度300mm/minで切断した例であるが、良好な切断面が得られた。アシストガスは0.6MPaのN2ガスで、レーザ波形は500Hz、Duty30%である。
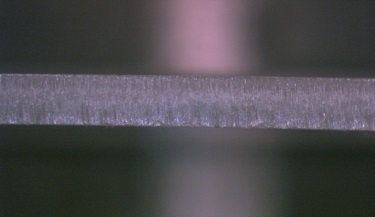
写真11 サファイヤガラスの切断
また同材の孔(穴)加工も行っているが、その際は1kHzでDuty10%のパルス波形を使用している。
従来、この材料は他の発振器での加工は困難であったが、高いエネルギー密度を照射できた結果、このような加工ができたものと考える。
5.おわりに
シングルモードファイバーレーザは近年3kW級まで高出力化が進み、にわかに注目を浴びているが、これにより理論限界に近いビーム品質が高出力で得られ、超高エネルギー密度の加工ができるようになった。言い換えれば、現実に直径15μmの所に数kWのレーザビームを照射することができるようになった。その結果、溶接、切断および孔(穴)・溝加工ではより超高速度な加工、高精密な加工が実現できるようになった。また異材溶接では従来と異なる溶融・凝固現象を示しているが、まだ未知の部分が多い。
本稿がものづくりエンジニヤの方々の参考になればこの上なく幸甚に存じます。
参考文献
1) 宮本、高出力ファイバーレーザによる加工、 O plus E、Vol.27, No.11, 2005-11
2) 荒谷、高出力ファイバーレーザとその加工特性、溶接技術、2006-8
3) IPG技術資料、2007
4) Morgenthal,L, Cutting with Fiber Lasers, 1st IFW, 2005-11
5) Himmer, T., High Brightness Laser in Cutting Applicasions, ICALEO, 2007-10
6) Seefeld,T, Welding with Fiber laser BLZ-Semminar, 2005-4
レーザ加工の事ならおまかせ!
本サイト運営会社レーザックスの紹介はこちら!
運営会社紹介ページへ
レーザに関する情報が盛りだくさん!
レーザ加工なびTOPへ