「溶接ニュース」 レーザ溶接編
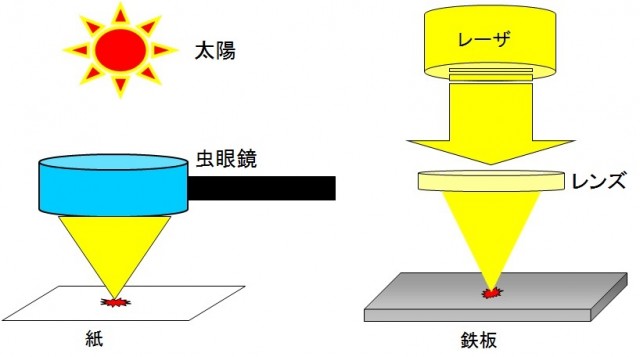
週刊「溶接ニュース」
「レーザ溶接編」より
株式会社レーザックス 新開潤子
1. レーザって何?
■「レーザ」という言葉の意味
私たちの周囲にある光は、虹で知られる赤、橙、黄、緑、青、藍、紫など可視光と、赤外線・紫外線など人間の目には見えない光が混合してできている。レーザはこの内の1色だけを取り出して増幅させた人工の光のことで、英語のLight Amplification by Stimulated Emission of Radiation(誘導放出による光の増幅)の頭文字を取った造語だ。
■レーザ加工の原理
小学校の理科の授業で、太陽の光を虫眼鏡で集めて黒い紙を焦がす実験をした人も多いだろう。レーザも同じ原理を使っていて、レーザをレンズで集光することで加工に使うエネルギーを得る。太陽光と虫眼鏡の実験では紙が焦げる程度だが、レーザを集光させると焦点で鉄板も簡単に溶かしてしまうような大きなパワーが得られる(図1)。これを加工に利用するのがレーザ加工だ。
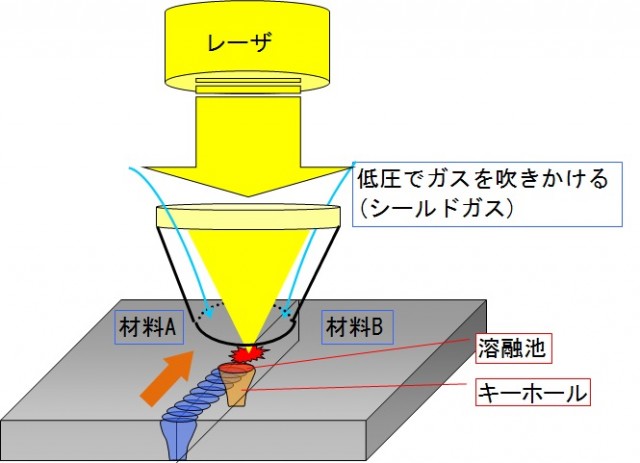
図1 レーザ加工の原理
例えばレーザを鉄板に当てると、レーザのエネルギーが鉄板の表面で吸収されて表面温度が上昇する。そのときレーザの出力と照射時間を調整し、表面温度を次の3つの状態のいずれかにコントロールするのがレーザ加工のポイントになる。
①加熱する
②融点まで温度を上げる
③沸点まで温度を上げる
①~③を適切に使い分けることで、レーザのパワーをさまざまな加工に活用することができる。
■レーザでできること
レーザ加工で最も多く活用されているのが、前項②の融点まで温度を上げて行う加工だ。2つ以上の部材を溶融させて一体化させるのがレーザ溶接、溶融した金属を高圧ガスで吹き飛ばして孔が開いたところでストップすれば孔あけ、そのまま連続して動かせば切断となる。
対象ワークが樹脂であれば樹脂溶着となり、最近では金属と樹脂の異材接合も実用化されてきている。その他にも、歪みが少なく高い硬さを得られるレーザ焼入れや、ワーク表面や樹脂やガラスの内部に文字や図柄を刻むレーザマーキング、汚れや塗膜を一瞬で飛ばすレーザクリーニングなど、活用の分野は多岐に渡っている。
2. レーザで行う溶接
■レーザ溶接の仕組み
レーザの高いパワー密度を活かして深溶込みが得られるキーホール型のレーザ溶接の基本的な仕組みについて図2に示した。レーザで材料Aと材料Bを溶接する場合、まずはレーザを集光して材料に照射し、材料の温度を融点まで上げて溶かす。溶けた材料Aと材料Bが溶融池を形成して混ざり合い、キーホールと呼ばれる溶融金属に囲まれた穴ができる。熱源の移動に伴い溶融金属はキーホールの周囲を流れ、溶融池の後部で凝固する。これが連続することで、連続した溶接部を得ることができる。
このとき、溶融金属が大気中の酸素に触れると反応し、溶接継手強度低下や変色の原因になる。それを防ぐため、レーザ溶接では加工点の周囲に低圧でガスを吹きかけて大気から保護するする。このガスをシールドガスと呼び、素材と反応しない窒素やアルゴンなどを使い分ける。また、ガス圧が高すぎると溶融金属を吹き飛ばしてしまうので、適正なガス圧に管理することも大切だ。
図2レーザ溶接の仕組み
■溶接条件の決め方
レーザ溶接で良い溶接結果を得るためには、レーザ、光学系、溶接条件、材料、シールドガスなどの要素とそれぞれの相関関係を把握し、管理することが必要になる(図3)。例えばレーザで言えば発振器の種類、レーザの波長、CW発振かパルス発振かなどの項目を吟味する。溶接条件については、レーザ出力、溶接速度、パルス幅と周波数、焦点外し距離などを都度検討する必要がある。
当社は約30台のレーザ加工機を保有しており、レーザ加工のジョブショップとして顧客からの依頼を受けて多種多様なレーザ加工を行っている。溶接の依頼を受ける場合、まず材料から加工に適したレーザ発振器を選定し、必要な溶込み深さからレーザ出力を判断する。そして継手の状況により使用する光学系を選定したうえで、実際にテスト加工を行って顧客要求を満たす溶接条件を求めている。
また、当社はレーザ光学系の機器としてレーザ加工ヘッドの設計製作も行っており、顧客の工場にレーザ加工システムを導入するお手伝いもさせていただいている。その場合、まずは溶接したいワークを持参いただいて前述の諸条件を検討し、当社所有のレーザ発振器と加工ヘッドを使って条件出しを実施する。求められた加工品質を実現できる溶接条件を確定してから納入するので、加工の再現性が高く、顧客の工場での生産にスムーズに移行することができる。
いずれの場合も机上の計算のみで最適な溶接条件を求めることは難しいので、テスト加工を並行して実施し、求める溶接品質を得られるかどうかを確認するようにしている。
図3 溶接継手品質に影響する各種因子
3. レーザ溶接の品質管理
■溶接欠陥の例
前述のように、レーザ溶接では様々な溶接条件が複雑に影響し合って良好な溶接結果を得られるが、裏を返せば条件が整わないと溶接欠陥が発生する可能性もある。ここに代表的な溶接欠陥の例を示す(図4)。
ポロシティは、キーホールの中で溶融金属中に発生したガスが凝固後の溶接部に取り込まれ、気泡として残ってしまう現象だ。いくつかの原因が考えられており、金属蒸気がキーホール内に残り気泡化するケース、シールドガスを巻き込んで気泡を形成するケースなどがあるが、材料の表面に油分や錆びなどが残っている場合にも発生しやすい。溶接前の前処理をきちんと行うという基本的な作業も大切だ。
レーザ溶接では金属に対して急熱急冷を行うこともあり、溶融部の熱ひずみにより溶接割れが発生する場合もある。原因は様々だが材質によるところも大きいので、正しい材料を選択することで溶接不良を回避できるケースもある。例えばステンレス鋼では、SUS303は切削性を向上させた材料なのでクラックが入りやすいため、溶接性に優れたSUS304のほうが望ましい。
他にもアンダーカットが発生すると、陥没部分が切り欠きになってクラックが入るきっかけになるし、アンダーフィルが発生すると溶接継手強度不足が懸念される。これらの溶接不良を防ぐためには、加工条件設定と品質検査を適切に実施していく必要がある。
図4 溶接欠陥の例
■ワークに対する品質検査
溶接という加工の性質上、品質検査は基本的に破壊検査になるが、検査の為に製品を全数破壊することはできない。そこで当社では、加工の初品、中間品、終品で抜き取り検査を実施し、正しく品質を把握し維持するよう努めている。
具体的には、ワークを切断して断面観察で溶込み深さと割れなどの状態を確認するほか、引張り試験やリークディテクターによる封止溶接後の漏れ確認などを組み合わせて実施する。
■レーザ溶接の生産品質維持
当社のレーザ溶接では、事前に定めた加工条件をワーク上で正確に実現することで生産品質を確保している。加工条件を正しく実現するためにはシステム側を適正に調整することが不可欠だが、実際に加工を行うレーザ光は目に見えないので、調整には専用の測定装置を使用してデータを可視化する必要がある。
パワーメータはレーザ出力を計測する装置で、レーザの出射光を受けて光の強さを数値で見ることができる。測定値が発振器側の出力よりも大幅に少ない場合、光学系(レンズ・保護ガラスなど)の汚損やレーザ発振器の異常を疑うことができるため、加工に入る前に必要な対策をとることができる。また、ビームの状態を観察するフォーカスモニタを使うと、焦点位置やビームの状態、エネルギー分布など目には見えないレーザ光の状態を確認することができる(図5)。
図5 ビームプロファイラの測定画面の例
これらの装置から得られる可視化されたデータを適切に活用すれば、加工条件をより正しく実現し、より確かな生産品質を確保することができる。
レーザ加工の事ならおまかせ!
本サイト運営会社レーザックスの紹介はこちら!
運営会社紹介ページへ
レーザに関する情報が盛りだくさん!
レーザ加工なびTOPへ
「レーザ溶接編」より
株式会社レーザックス 新開潤子
1. レーザって何?
■「レーザ」という言葉の意味
私たちの周囲にある光は、虹で知られる赤、橙、黄、緑、青、藍、紫など可視光と、赤外線・紫外線など人間の目には見えない光が混合してできている。レーザはこの内の1色だけを取り出して増幅させた人工の光のことで、英語のLight Amplification by Stimulated Emission of Radiation(誘導放出による光の増幅)の頭文字を取った造語だ。
■レーザ加工の原理
小学校の理科の授業で、太陽の光を虫眼鏡で集めて黒い紙を焦がす実験をした人も多いだろう。レーザも同じ原理を使っていて、レーザをレンズで集光することで加工に使うエネルギーを得る。太陽光と虫眼鏡の実験では紙が焦げる程度だが、レーザを集光させると焦点で鉄板も簡単に溶かしてしまうような大きなパワーが得られる(図1)。これを加工に利用するのがレーザ加工だ。
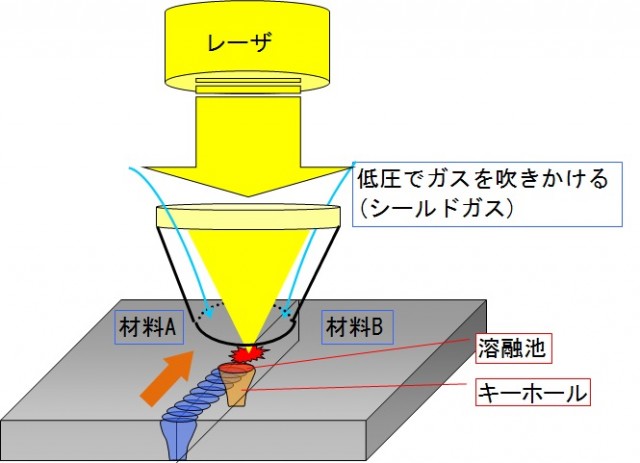
図1 レーザ加工の原理
例えばレーザを鉄板に当てると、レーザのエネルギーが鉄板の表面で吸収されて表面温度が上昇する。そのときレーザの出力と照射時間を調整し、表面温度を次の3つの状態のいずれかにコントロールするのがレーザ加工のポイントになる。
①加熱する
②融点まで温度を上げる
③沸点まで温度を上げる
①~③を適切に使い分けることで、レーザのパワーをさまざまな加工に活用することができる。
■レーザでできること
レーザ加工で最も多く活用されているのが、前項②の融点まで温度を上げて行う加工だ。2つ以上の部材を溶融させて一体化させるのがレーザ溶接、溶融した金属を高圧ガスで吹き飛ばして孔が開いたところでストップすれば孔あけ、そのまま連続して動かせば切断となる。
対象ワークが樹脂であれば樹脂溶着となり、最近では金属と樹脂の異材接合も実用化されてきている。その他にも、歪みが少なく高い硬さを得られるレーザ焼入れや、ワーク表面や樹脂やガラスの内部に文字や図柄を刻むレーザマーキング、汚れや塗膜を一瞬で飛ばすレーザクリーニングなど、活用の分野は多岐に渡っている。
2. レーザで行う溶接
■レーザ溶接の仕組み
レーザの高いパワー密度を活かして深溶込みが得られるキーホール型のレーザ溶接の基本的な仕組みについて図2に示した。レーザで材料Aと材料Bを溶接する場合、まずはレーザを集光して材料に照射し、材料の温度を融点まで上げて溶かす。溶けた材料Aと材料Bが溶融池を形成して混ざり合い、キーホールと呼ばれる溶融金属に囲まれた穴ができる。熱源の移動に伴い溶融金属はキーホールの周囲を流れ、溶融池の後部で凝固する。これが連続することで、連続した溶接部を得ることができる。
このとき、溶融金属が大気中の酸素に触れると反応し、溶接継手強度低下や変色の原因になる。それを防ぐため、レーザ溶接では加工点の周囲に低圧でガスを吹きかけて大気から保護するする。このガスをシールドガスと呼び、素材と反応しない窒素やアルゴンなどを使い分ける。また、ガス圧が高すぎると溶融金属を吹き飛ばしてしまうので、適正なガス圧に管理することも大切だ。
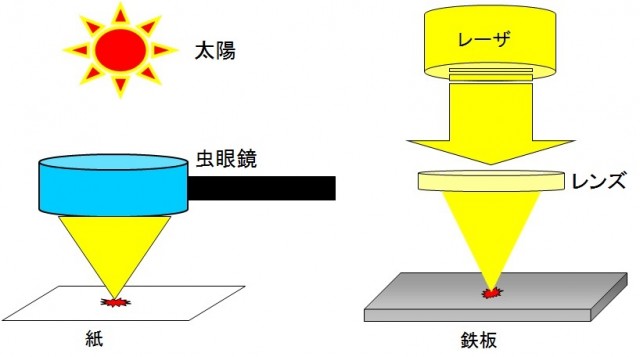
図2レーザ溶接の仕組み
■溶接条件の決め方
レーザ溶接で良い溶接結果を得るためには、レーザ、光学系、溶接条件、材料、シールドガスなどの要素とそれぞれの相関関係を把握し、管理することが必要になる(図3)。例えばレーザで言えば発振器の種類、レーザの波長、CW発振かパルス発振かなどの項目を吟味する。溶接条件については、レーザ出力、溶接速度、パルス幅と周波数、焦点外し距離などを都度検討する必要がある。
当社は約30台のレーザ加工機を保有しており、レーザ加工のジョブショップとして顧客からの依頼を受けて多種多様なレーザ加工を行っている。溶接の依頼を受ける場合、まず材料から加工に適したレーザ発振器を選定し、必要な溶込み深さからレーザ出力を判断する。そして継手の状況により使用する光学系を選定したうえで、実際にテスト加工を行って顧客要求を満たす溶接条件を求めている。
また、当社はレーザ光学系の機器としてレーザ加工ヘッドの設計製作も行っており、顧客の工場にレーザ加工システムを導入するお手伝いもさせていただいている。その場合、まずは溶接したいワークを持参いただいて前述の諸条件を検討し、当社所有のレーザ発振器と加工ヘッドを使って条件出しを実施する。求められた加工品質を実現できる溶接条件を確定してから納入するので、加工の再現性が高く、顧客の工場での生産にスムーズに移行することができる。
いずれの場合も机上の計算のみで最適な溶接条件を求めることは難しいので、テスト加工を並行して実施し、求める溶接品質を得られるかどうかを確認するようにしている。
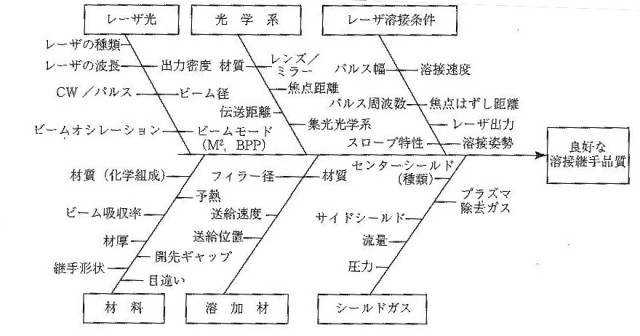
図3 溶接継手品質に影響する各種因子
3. レーザ溶接の品質管理
■溶接欠陥の例
前述のように、レーザ溶接では様々な溶接条件が複雑に影響し合って良好な溶接結果を得られるが、裏を返せば条件が整わないと溶接欠陥が発生する可能性もある。ここに代表的な溶接欠陥の例を示す(図4)。
ポロシティは、キーホールの中で溶融金属中に発生したガスが凝固後の溶接部に取り込まれ、気泡として残ってしまう現象だ。いくつかの原因が考えられており、金属蒸気がキーホール内に残り気泡化するケース、シールドガスを巻き込んで気泡を形成するケースなどがあるが、材料の表面に油分や錆びなどが残っている場合にも発生しやすい。溶接前の前処理をきちんと行うという基本的な作業も大切だ。
レーザ溶接では金属に対して急熱急冷を行うこともあり、溶融部の熱ひずみにより溶接割れが発生する場合もある。原因は様々だが材質によるところも大きいので、正しい材料を選択することで溶接不良を回避できるケースもある。例えばステンレス鋼では、SUS303は切削性を向上させた材料なのでクラックが入りやすいため、溶接性に優れたSUS304のほうが望ましい。
他にもアンダーカットが発生すると、陥没部分が切り欠きになってクラックが入るきっかけになるし、アンダーフィルが発生すると溶接継手強度不足が懸念される。これらの溶接不良を防ぐためには、加工条件設定と品質検査を適切に実施していく必要がある。
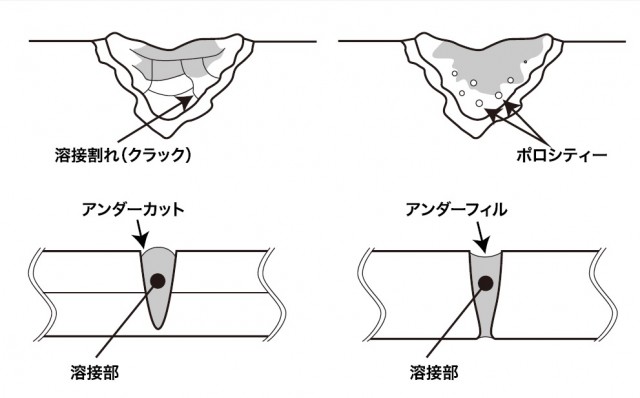
図4 溶接欠陥の例
■ワークに対する品質検査
溶接という加工の性質上、品質検査は基本的に破壊検査になるが、検査の為に製品を全数破壊することはできない。そこで当社では、加工の初品、中間品、終品で抜き取り検査を実施し、正しく品質を把握し維持するよう努めている。
具体的には、ワークを切断して断面観察で溶込み深さと割れなどの状態を確認するほか、引張り試験やリークディテクターによる封止溶接後の漏れ確認などを組み合わせて実施する。
■レーザ溶接の生産品質維持
当社のレーザ溶接では、事前に定めた加工条件をワーク上で正確に実現することで生産品質を確保している。加工条件を正しく実現するためにはシステム側を適正に調整することが不可欠だが、実際に加工を行うレーザ光は目に見えないので、調整には専用の測定装置を使用してデータを可視化する必要がある。
パワーメータはレーザ出力を計測する装置で、レーザの出射光を受けて光の強さを数値で見ることができる。測定値が発振器側の出力よりも大幅に少ない場合、光学系(レンズ・保護ガラスなど)の汚損やレーザ発振器の異常を疑うことができるため、加工に入る前に必要な対策をとることができる。また、ビームの状態を観察するフォーカスモニタを使うと、焦点位置やビームの状態、エネルギー分布など目には見えないレーザ光の状態を確認することができる(図5)。
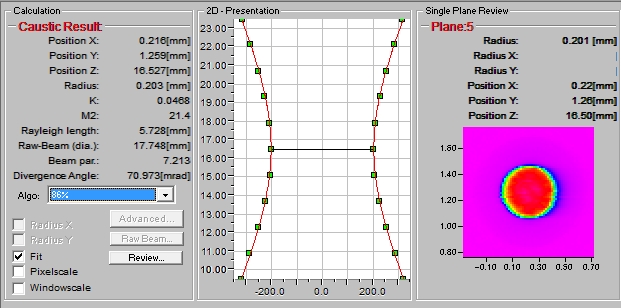
図5 ビームプロファイラの測定画面の例
これらの装置から得られる可視化されたデータを適切に活用すれば、加工条件をより正しく実現し、より確かな生産品質を確保することができる。
レーザ加工の事ならおまかせ!
本サイト運営会社レーザックスの紹介はこちら!
運営会社紹介ページへ
レーザに関する情報が盛りだくさん!
レーザ加工なびTOPへ