ファイバーレーザ加工機による航空機部品などへの孔あけ
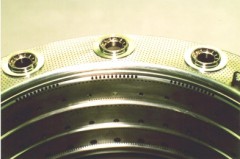
月刊ツールエンジニア 2016年5月号より
「ファイバーレーザ加工機による航空機部品などへの孔あけ」
株式会社レーザックス 池田 剛司
1.はじめに
航空機部品においてジェットエンジン部品等の孔あけにレーザが実用化されているが、これら孔あけ加工には高ピークパルス発振が可能なランプ励起Nd:YAGレーザを搭載した3次元同時6軸制御加工機が採用されてきた。しかしこのランプ励起Nd:YAGレーザは、ビーム品質(集光性)が悪く、電気/光エネルギー変換効率も2~4%と極めて低いという欠点があった。近年、ビーム品質、電気・光変換効率が大幅に改善され高ピークパルス発振が可能なファイバーレーザ発振器が開発された。従来のパルスNd:YAGレーザに代わり、航空機部品など深孔加工用の発振器として注目されている。ここでは、ファイバーレーザ加工機による航空機部品などへの孔あけと題し、近年の取り組み事例について紹介する。
2.航空機産業への取り組み
当社は1984年にレーザ加工機による受託加工業、いわゆるレーザジョブショップに参入した。そのころはまさにレーザジョブショップの黎明期といえる時期だが、出力1kWまでの炭酸ガスレーザを搭載した板金切断用の二次元加工機が主力であった。
その後1991年に、ルモニクス(現GSIグループ)社製パルスNd:YAGレーザJK704を搭載した孔あけ用3次元6軸同期制御加工機Laserdyne780を導入して航空機ジェットエンジン、及び発電用ガスタービンエンジン部品への加工に取り組み始めた。
ジェットエンジンの効率向上には、その動作温度を上昇させることが最も有効である。耐熱合金により製造されているとはいえ極めて過酷な動作・使用環境であるため、高性能な冷却技術や伝熱制御技術が利用されている。その代表が「フィルム冷却技術」であり、ジェットエンジン部品には、非常に多くの冷却用孔あけが施される。
これらの受託加工は、当初は顧客ごとに品質保証認定を取得して活動してきた。しかし、航空機産業においてレーザ加工は特殊工程(製造の結果がその後に検査できない工程、または引渡し後にしか不具合がわからない工程)の一つとして位置づけられており、国際的航空宇宙防衛産業特殊工程認証プログラムNadcapの認証取得が義務付けられる場合が増えてきた。そのため当社では2008年のAS9100 Rev.B認証取得を経て、2009年にNadcap(特殊機械加工)認証を取得して社内体制を整えてきた。
航空機部品は大きく分けて「機体」「装備品」「エンジン」の3つに分類される。エンジンについては、欧米の3大メーカー(GE、P&W、RR)がこの市場を寡占している。そして日本のIHI、三菱重工業、川崎重工業はTier1(一次サプライヤ)として、燃焼器モジュール等の主要構成部品を開発・生産している。その傘下でTier2(二次サプライヤ)は、エンジンの材料や構成部品の供給・加工等を行う(2)。当社は、エンジンメーカーのTier2として航空機産業の一端を担ってきた。一方、機体及び装備品の分野でいわれていることだが、部品供給責任は、最後の5機が運用されるまでとされている。そうなると、生産20年運用30年の合計50年が部品供給責任となり、非常に長期に亘る(3)。
航空機産業への取り組みは非常に長期間の活動となるのだが、その間にも生産設備は老朽するので更新していかねばならない。1991年に導入した孔あけ用3次元6軸同期制御加工機Laserdyne780は、ルモニクス社製パルスNd:YAGレーザJK704のアフターサービスが2015年末に終了した。そのため新型機導入に踏み切り、2015年にはIPG社QCWファイバーレーザを搭載した新型加工機のLaserdyne795を導入するに至った(図2)。
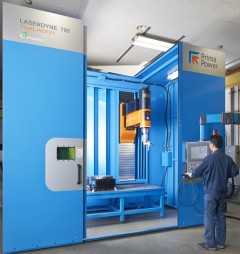
図2 Laserdyne795装置外観
3.加工事例
ここでは、新型加工機Laserdyne795による加工事例を紹介する。
レーザは光なので、ドリル加工などのような接触加工ではなく、非接触加工である。そのため、ワーク形状がレーザ入射方向に対して斜めであっても、曲面であっても加工でき、ワーク形状にあまり左右されない。この特徴を示す例として、ステンレス鋼SUS304の板厚10mmに対して、垂直方向から60度斜め入射により直径約1mmの貫通孔加工を施した加工事例を図3に示す。孔加工はトレパニングといって、あけたい孔の輪郭に沿ってレーザ照射する加工方法で行った。様々な孔径や形状を加工でき、孔形状の安定性の面で優れている。何周も走査することによって厚板加工が可能である。
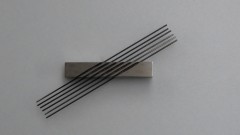
斜め孔あけサンプル
この加工機は3次元でありながら直交軸の位置決め精度は±20μmと非常に高精度である。この特徴を示す例として、外径100mm、板厚2mmのステンレス鋼SUS304パイプに対して、入射角度を変化させながら肉厚約0.5mmを残して格子状に孔あけを行った加工事例を図4に示す。これだけの高密度に孔加工を行っても、熱によるひずみの発生は見られなかった。
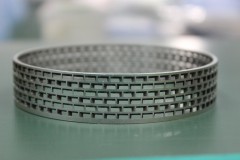
図4 パイプへの斜め格子孔あけ
航空機部品であるタービンブレードを模擬したサンプルの製作事例を図5に示す。ジェットエンジンで実際に使用される材料は耐熱合金だが、模擬サンプルはステンレス鋼SUS304で製作した。図で示したサンプルの裏側にも加工すべき箇所があるのだが、6軸制御加工機の特徴を生かし、段取り変更なしで加工した。
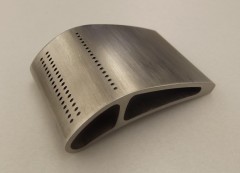
図5 タービンブレード模擬サンプル
4.難加工材の加工特性
航空機部品加工では耐熱合金など、いわゆる難加工材を対象にする場合が多い。この難加工材という表現は切削加工分野で用いられるが、レーザ熱加工ではどうなるか、という観点で基本的な加工特性を調査した内容についてまとめた(4)。
調査した材料は、ステンレス鋼(オーステナイト系、SUS304)、軟鋼(一般構造用圧延鋼材、SS400)、アルミニウム合金(Al-Mg系、A5052)、銅合金(タフピッチ銅、C1100)と、耐熱合金としてNi基のハステロイの5種類である。
レーザ熱加工でも切削加工でも、熱伝導率の影響が非常に大きい。まずレーザ熱加工での加熱は極表層で起こり、この熱は材料内へ熱伝導で伝達される。
切削加工では被削率といって、材料の削られやすさ(難しさ)を切削工具の寿命に及ぼす影響から評価した値がある。これは、低炭素硫黄快削鋼(JISではSUM21が相当材)を基準材料とし、切削速度約60m/minで一定時間切削したときの切削工具の逃げ面磨耗幅を基準材料と比較した値である。ハステロイなどの耐熱合金では、被削率が10程度ともいわれ切削加工においては難加工材である。切削加工中に発生する熱が工具寿命を縮める要因ともなっているので、熱伝導率が低い材料は工具寿命が短くなる傾向、すなわち、被削率が低下する傾向がある。このように、熱伝導率はレーザ熱加工、切削加工の双方に大きな影響を及ぼし、加工特性への影響は相対する。
ここではファイバーレーザでのシングルショット照射による非貫通孔加工の特性を調査した。孔が板厚を貫通しないので、溶融・蒸発した金属材料はレーザ照射方向とは逆方向に噴出しながら除去されるため、その加工特性には密度の影響も受けると考えられる。
これらのファイバーレーザによる孔加工特性をまとめたものを、表1及び図6に示す。ステンレス鋼、軟鋼及び耐熱合金の3種類がほぼ同じ加工特性となった。耐熱合金は熱伝導率が小さいので切削加工では難加工材だが、レーザ熱加工ではステンレス鋼や軟鋼と同等だった。
アルミニウム合金は、前述の3種類と同等以上の孔加工特性を示した。密度が非常に小さいことに理由があると考えられる。銅合金は、熱伝導率が非常に高いのと、密度が前述の3種類よりも大きいことが影響して、穴加工特性は最も劣っていた。銅合金はレーザ熱加工では難加工材であることがわかった。
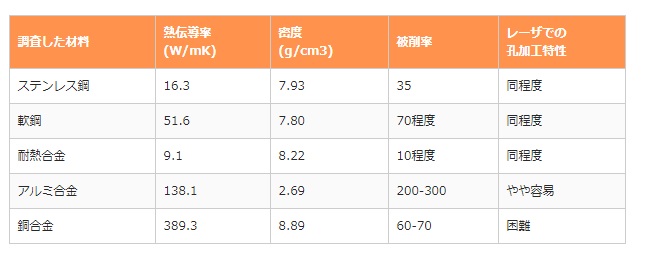
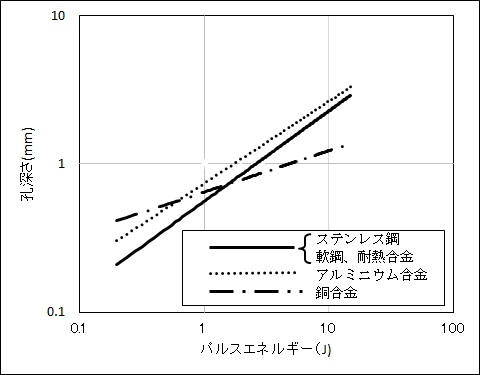
図6 ファイバーレーザによる孔加工特性
5.おわりに
ここでは金属材料について、サンプル加工事例や加工特性を示した。切削加工では難加工材とされる耐熱合金も、レーザ熱加工ではステンレス鋼や軟鋼と同等であることを示した。今後はセラミックスなど他の難加工材に対しても、適用範囲拡大の可能性を追求していきたい。
参考文献
(1)坪井昭彦、ツールエンジニア、第54巻、第13号、(2013年10月)、大河出版、40-43
(2)海上泰生、日本政策金融公庫論集、第11号、(2011年5 月)、21-46
(3)高橋教雄、航空機部品供給システム研究会、第16回定例講演会、(2014年8月6日)
(4)池田剛司、第84回レーザ加工学会講演論文集、(2016年1月20日)、167-170
レーザ加工の事ならおまかせ!
本サイト運営会社レーザックスの紹介はこちら!
運営会社紹介ページへ
レーザに関する情報が盛りだくさん!
レーザ加工なびTOPへ
「ファイバーレーザ加工機による航空機部品などへの孔あけ」
株式会社レーザックス 池田 剛司
1.はじめに
航空機部品においてジェットエンジン部品等の孔あけにレーザが実用化されているが、これら孔あけ加工には高ピークパルス発振が可能なランプ励起Nd:YAGレーザを搭載した3次元同時6軸制御加工機が採用されてきた。しかしこのランプ励起Nd:YAGレーザは、ビーム品質(集光性)が悪く、電気/光エネルギー変換効率も2~4%と極めて低いという欠点があった。近年、ビーム品質、電気・光変換効率が大幅に改善され高ピークパルス発振が可能なファイバーレーザ発振器が開発された。従来のパルスNd:YAGレーザに代わり、航空機部品など深孔加工用の発振器として注目されている。ここでは、ファイバーレーザ加工機による航空機部品などへの孔あけと題し、近年の取り組み事例について紹介する。
2.航空機産業への取り組み
当社は1984年にレーザ加工機による受託加工業、いわゆるレーザジョブショップに参入した。そのころはまさにレーザジョブショップの黎明期といえる時期だが、出力1kWまでの炭酸ガスレーザを搭載した板金切断用の二次元加工機が主力であった。
その後1991年に、ルモニクス(現GSIグループ)社製パルスNd:YAGレーザJK704を搭載した孔あけ用3次元6軸同期制御加工機Laserdyne780を導入して航空機ジェットエンジン、及び発電用ガスタービンエンジン部品への加工に取り組み始めた。
ジェットエンジンの効率向上には、その動作温度を上昇させることが最も有効である。耐熱合金により製造されているとはいえ極めて過酷な動作・使用環境であるため、高性能な冷却技術や伝熱制御技術が利用されている。その代表が「フィルム冷却技術」であり、ジェットエンジン部品には、非常に多くの冷却用孔あけが施される。
これらの受託加工は、当初は顧客ごとに品質保証認定を取得して活動してきた。しかし、航空機産業においてレーザ加工は特殊工程(製造の結果がその後に検査できない工程、または引渡し後にしか不具合がわからない工程)の一つとして位置づけられており、国際的航空宇宙防衛産業特殊工程認証プログラムNadcapの認証取得が義務付けられる場合が増えてきた。そのため当社では2008年のAS9100 Rev.B認証取得を経て、2009年にNadcap(特殊機械加工)認証を取得して社内体制を整えてきた。
航空機部品は大きく分けて「機体」「装備品」「エンジン」の3つに分類される。エンジンについては、欧米の3大メーカー(GE、P&W、RR)がこの市場を寡占している。そして日本のIHI、三菱重工業、川崎重工業はTier1(一次サプライヤ)として、燃焼器モジュール等の主要構成部品を開発・生産している。その傘下でTier2(二次サプライヤ)は、エンジンの材料や構成部品の供給・加工等を行う(2)。当社は、エンジンメーカーのTier2として航空機産業の一端を担ってきた。一方、機体及び装備品の分野でいわれていることだが、部品供給責任は、最後の5機が運用されるまでとされている。そうなると、生産20年運用30年の合計50年が部品供給責任となり、非常に長期に亘る(3)。
航空機産業への取り組みは非常に長期間の活動となるのだが、その間にも生産設備は老朽するので更新していかねばならない。1991年に導入した孔あけ用3次元6軸同期制御加工機Laserdyne780は、ルモニクス社製パルスNd:YAGレーザJK704のアフターサービスが2015年末に終了した。そのため新型機導入に踏み切り、2015年にはIPG社QCWファイバーレーザを搭載した新型加工機のLaserdyne795を導入するに至った(図2)。
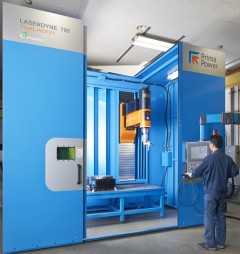
図2 Laserdyne795装置外観
3.加工事例
ここでは、新型加工機Laserdyne795による加工事例を紹介する。
レーザは光なので、ドリル加工などのような接触加工ではなく、非接触加工である。そのため、ワーク形状がレーザ入射方向に対して斜めであっても、曲面であっても加工でき、ワーク形状にあまり左右されない。この特徴を示す例として、ステンレス鋼SUS304の板厚10mmに対して、垂直方向から60度斜め入射により直径約1mmの貫通孔加工を施した加工事例を図3に示す。孔加工はトレパニングといって、あけたい孔の輪郭に沿ってレーザ照射する加工方法で行った。様々な孔径や形状を加工でき、孔形状の安定性の面で優れている。何周も走査することによって厚板加工が可能である。
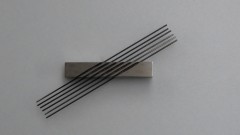
斜め孔あけサンプル
この加工機は3次元でありながら直交軸の位置決め精度は±20μmと非常に高精度である。この特徴を示す例として、外径100mm、板厚2mmのステンレス鋼SUS304パイプに対して、入射角度を変化させながら肉厚約0.5mmを残して格子状に孔あけを行った加工事例を図4に示す。これだけの高密度に孔加工を行っても、熱によるひずみの発生は見られなかった。
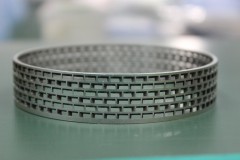
図4 パイプへの斜め格子孔あけ
航空機部品であるタービンブレードを模擬したサンプルの製作事例を図5に示す。ジェットエンジンで実際に使用される材料は耐熱合金だが、模擬サンプルはステンレス鋼SUS304で製作した。図で示したサンプルの裏側にも加工すべき箇所があるのだが、6軸制御加工機の特徴を生かし、段取り変更なしで加工した。
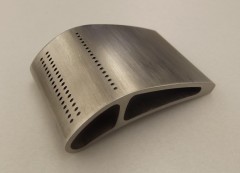
図5 タービンブレード模擬サンプル
4.難加工材の加工特性
航空機部品加工では耐熱合金など、いわゆる難加工材を対象にする場合が多い。この難加工材という表現は切削加工分野で用いられるが、レーザ熱加工ではどうなるか、という観点で基本的な加工特性を調査した内容についてまとめた(4)。
調査した材料は、ステンレス鋼(オーステナイト系、SUS304)、軟鋼(一般構造用圧延鋼材、SS400)、アルミニウム合金(Al-Mg系、A5052)、銅合金(タフピッチ銅、C1100)と、耐熱合金としてNi基のハステロイの5種類である。
レーザ熱加工でも切削加工でも、熱伝導率の影響が非常に大きい。まずレーザ熱加工での加熱は極表層で起こり、この熱は材料内へ熱伝導で伝達される。
切削加工では被削率といって、材料の削られやすさ(難しさ)を切削工具の寿命に及ぼす影響から評価した値がある。これは、低炭素硫黄快削鋼(JISではSUM21が相当材)を基準材料とし、切削速度約60m/minで一定時間切削したときの切削工具の逃げ面磨耗幅を基準材料と比較した値である。ハステロイなどの耐熱合金では、被削率が10程度ともいわれ切削加工においては難加工材である。切削加工中に発生する熱が工具寿命を縮める要因ともなっているので、熱伝導率が低い材料は工具寿命が短くなる傾向、すなわち、被削率が低下する傾向がある。このように、熱伝導率はレーザ熱加工、切削加工の双方に大きな影響を及ぼし、加工特性への影響は相対する。
ここではファイバーレーザでのシングルショット照射による非貫通孔加工の特性を調査した。孔が板厚を貫通しないので、溶融・蒸発した金属材料はレーザ照射方向とは逆方向に噴出しながら除去されるため、その加工特性には密度の影響も受けると考えられる。
これらのファイバーレーザによる孔加工特性をまとめたものを、表1及び図6に示す。ステンレス鋼、軟鋼及び耐熱合金の3種類がほぼ同じ加工特性となった。耐熱合金は熱伝導率が小さいので切削加工では難加工材だが、レーザ熱加工ではステンレス鋼や軟鋼と同等だった。
アルミニウム合金は、前述の3種類と同等以上の孔加工特性を示した。密度が非常に小さいことに理由があると考えられる。銅合金は、熱伝導率が非常に高いのと、密度が前述の3種類よりも大きいことが影響して、穴加工特性は最も劣っていた。銅合金はレーザ熱加工では難加工材であることがわかった。
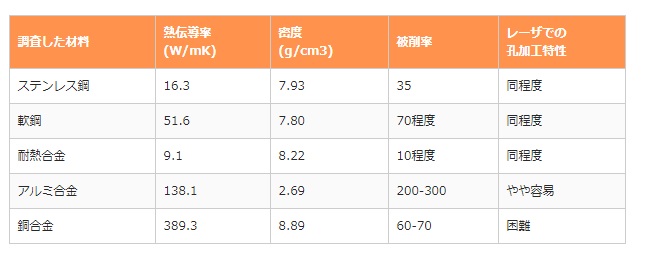
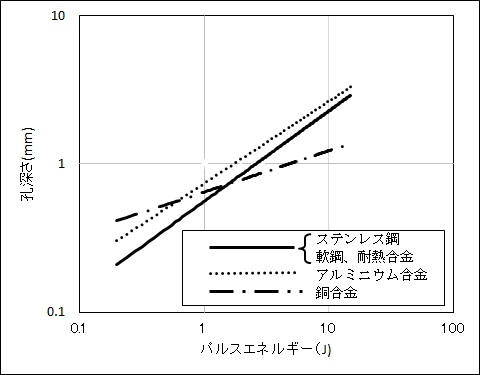
図6 ファイバーレーザによる孔加工特性
5.おわりに
ここでは金属材料について、サンプル加工事例や加工特性を示した。切削加工では難加工材とされる耐熱合金も、レーザ熱加工ではステンレス鋼や軟鋼と同等であることを示した。今後はセラミックスなど他の難加工材に対しても、適用範囲拡大の可能性を追求していきたい。
参考文献
(1)坪井昭彦、ツールエンジニア、第54巻、第13号、(2013年10月)、大河出版、40-43
(2)海上泰生、日本政策金融公庫論集、第11号、(2011年5 月)、21-46
(3)高橋教雄、航空機部品供給システム研究会、第16回定例講演会、(2014年8月6日)
(4)池田剛司、第84回レーザ加工学会講演論文集、(2016年1月20日)、167-170
レーザ加工の事ならおまかせ!
本サイト運営会社レーザックスの紹介はこちら!
運営会社紹介ページへ
レーザに関する情報が盛りだくさん!
レーザ加工なびTOPへ